Water spray propulsion unit for ship
A water-jet propulsion, marine technology, applied in ship propulsion, propulsion components, ship construction, etc., can solve the problems of large impeller size, no self-priming ability, large thrust, etc., to ensure stability and maneuverability , The effect of diverse placement positions and enhanced slewing performance
- Summary
- Abstract
- Description
- Claims
- Application Information
AI Technical Summary
Problems solved by technology
Method used
Image
Examples
Embodiment Construction
[0083] Label in the figure
[0084] 1 pump body 2 pump body 3 pump body 4 pump body
[0085] 5 Partition plate assembly 6 Front end cover assembly 7 Rear end cover assembly
[0086]8 central axis 801 front axle head 802 rear axle head
[0087] 9 magazines 901 opening 902 opening
[0088] 900 peripheral flange 10 shell
[0089] 101 side flange 102 side flange 103 bottom flange
[0090] 11 Eccentric sleeve 111 Eccentric hole 112 Keyway
[0091] 12 rotor 120C-shaped notch groove 121 center hole
[0092] 122 front bearing chamber 123 rear bearing chamber 124 front bearing 125 rear bearing
[0093] 13 baffle plate 131 upper limit shaft 132 lower limit shaft
[0094] 14 Piston 140V-shaped notch groove 15 Working chamber
[0095] 151 chassis 152 motor 153 liquid inlet pipe
[0096] 154 intake pipe 155 rotary positive displacement pump 156 storage battery
[0097] 157 belt pulley 158 belt pulley 159 transmission belt 16 piston cavity
[0098] 17 fluid input channel 171 upst...
PUM
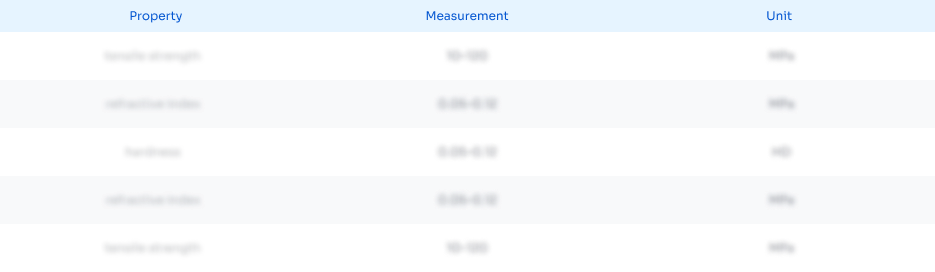
Abstract
Description
Claims
Application Information

- R&D
- Intellectual Property
- Life Sciences
- Materials
- Tech Scout
- Unparalleled Data Quality
- Higher Quality Content
- 60% Fewer Hallucinations
Browse by: Latest US Patents, China's latest patents, Technical Efficacy Thesaurus, Application Domain, Technology Topic, Popular Technical Reports.
© 2025 PatSnap. All rights reserved.Legal|Privacy policy|Modern Slavery Act Transparency Statement|Sitemap|About US| Contact US: help@patsnap.com