Welding method for non-coating sides of airship capsule material
A processing method and non-coating technology, which is applied in the field of welding and processing of aircraft capsule materials, can solve problems such as difficult sticking, difficulty in ensuring processing quality, and inability to control the ambient temperature and humidity of large-scale aircraft processing plants.
- Summary
- Abstract
- Description
- Claims
- Application Information
AI Technical Summary
Problems solved by technology
Method used
Examples
Embodiment Construction
[0016] In the research and development of the tethered airship of our unit, the method of the present invention is successfully used to complete the processing of the product. The air tightness of the welded part of the non-coated surface of the product is no more than 10% lower than that of the airbag material, and the tensile strength is comparable to that of the airbag. The material is reduced by no more than 10%. Specific steps are as follows:
[0017] 1. Surface treatment of non-coated surface of composite materials
[0018] The main airbag material used in this tethered airship is aramid polymer composite material. The non-coated surface of the material needs to be surface treated before coating the adhesive. The surface treatment includes: dip cotton with alcohol to remove surface dust, ethyl acetate Grease and acetone to remove surface oil stains, and ultrasonically activate the bonding surface. After the material is surface treated, it is transferred to the next pro...
PUM
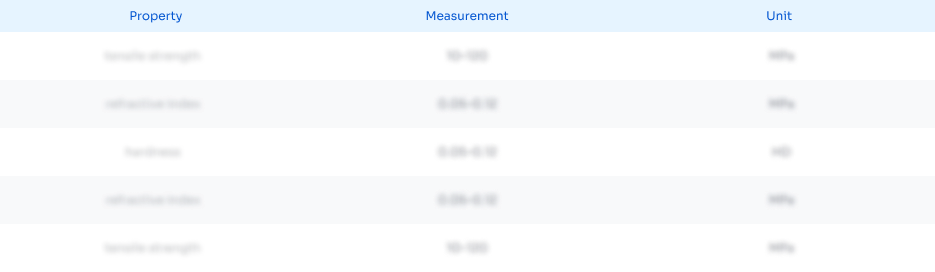
Abstract
Description
Claims
Application Information

- Generate Ideas
- Intellectual Property
- Life Sciences
- Materials
- Tech Scout
- Unparalleled Data Quality
- Higher Quality Content
- 60% Fewer Hallucinations
Browse by: Latest US Patents, China's latest patents, Technical Efficacy Thesaurus, Application Domain, Technology Topic, Popular Technical Reports.
© 2025 PatSnap. All rights reserved.Legal|Privacy policy|Modern Slavery Act Transparency Statement|Sitemap|About US| Contact US: help@patsnap.com