Thermoplastic elastomer micropore foaming material and preparation method thereof
A technology of thermoplastic elastomers and microcellular foam materials, which is applied in the field of rail transit and can solve problems such as few researches
- Summary
- Abstract
- Description
- Claims
- Application Information
AI Technical Summary
Problems solved by technology
Method used
Image
Examples
Embodiment 1
[0032] Select recipe 1 in the recipe table, the steps are as follows:
[0033] 1) Put the compatibilizer in a double-roll mill (roller temperature 80°C), add foaming agent and auxiliary foaming agent at the same time after masticating for 3 minutes, and knead for 5 minutes to prepare a foaming agent masterbatch.
[0034] 2) Add rubber, active agent, reinforcing filler, softener, vulcanizing agent and accelerator into the open mill at a temperature of 60°C in sequence, mix for 25 minutes, and disperse evenly to prepare a mixed rubber.
[0035] 3) After the mixed rubber is chopped and processed, it is evenly mixed with the plastic through a high-speed mixer, and extruded and granulated by an extruder to prepare TPV pellets. 150°C, 160°C in the third zone, 170°C in the fourth zone, 160°C in the fifth zone, and the screw speed is 30rpm.
[0036] 4) After pulverizing the foaming agent masterbatch obtained in step 1) and uniformly mixing the TPV pellets obtained in step 3) with a h...
Embodiment 2
[0038] Select recipe 2 in the recipe table, the steps are as follows:
[0039] (1) Put the compatibilizer in a two-roll mill (roller temperature 100°C), add foaming agent and auxiliary foaming agent at the same time after masticating for 1 minute, and knead for 3 minutes to prepare a foaming agent masterbatch.
[0040] (2) Add rubber, active agent, reinforcing filler, softener, vulcanizing agent and accelerator to the internal mixer in sequence, at a temperature of 80°C, at a rotor speed of 100r / min, and knead for about 10 minutes until the dispersion is uniform. into rubber compound.
[0041] (3) Chop the mixed rubber and mix it evenly with plastics, and prepare TPV pellets after extruding and granulating with an extruder. Zone 160°C, zone 4 160°C, zone 5 160°C, screw speed 90rpm.
[0042](4) After the thermoplastic vulcanizate and foaming agent masterbatch are pulverized and mixed uniformly by a high-speed mixer, they are extruded and shaped by a twin-screw extruder to obt...
Embodiment 3
[0044] Select formula 3 in the formula table, the steps are as follows:
[0045] (1) Put the compatibilizer in a double-roll mill (roller temperature 90°C), add foaming agent and auxiliary foaming agent at the same time after masticating for 2 minutes, and knead for 8 minutes to prepare a foaming agent masterbatch.
[0046] (2) Put rubber, active agent, reinforcing filler, softener, vulcanizing agent and accelerator into the open mill at 60°C in sequence, knead for about 20 minutes, and disperse evenly to prepare a mixed rubber.
[0047] (3) Chop the mixed rubber and mix it evenly with plastics, and prepare TPV pellets after extruding and granulating with an extruder. Zone 130°C, zone 4 140°C, zone 5 140°C, screw speed 60rpm.
[0048] (4) After the thermoplastic vulcanizate and foaming agent masterbatch are pulverized and mixed uniformly by a high-speed mixer, they are extruded and shaped by a twin-screw extruder to obtain a high-performance microcellular foaming material. A...
PUM
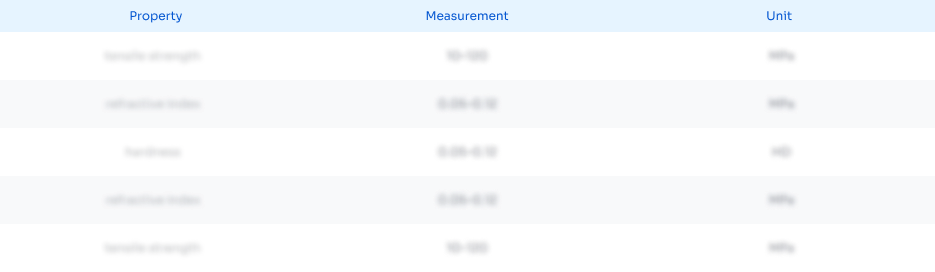
Abstract
Description
Claims
Application Information

- R&D
- Intellectual Property
- Life Sciences
- Materials
- Tech Scout
- Unparalleled Data Quality
- Higher Quality Content
- 60% Fewer Hallucinations
Browse by: Latest US Patents, China's latest patents, Technical Efficacy Thesaurus, Application Domain, Technology Topic, Popular Technical Reports.
© 2025 PatSnap. All rights reserved.Legal|Privacy policy|Modern Slavery Act Transparency Statement|Sitemap|About US| Contact US: help@patsnap.com