Multi-sensor fusion type fault locating method for gearbox of wind turbine generator
A multi-sensor fusion, wind turbine technology, applied in the direction of machine gear/transmission mechanism testing, etc., can solve problems such as unfavorable fault location, difficulty in gearbox fault location, and large vibration attenuation of faulty components.
- Summary
- Abstract
- Description
- Claims
- Application Information
AI Technical Summary
Problems solved by technology
Method used
Image
Examples
Embodiment Construction
[0044] The present invention will be described in further detail in conjunction with specific examples and accompanying drawings, but the embodiments of the present invention are not limited thereto.
[0045] Such as figure 1 As shown, the present invention is a multi-sensor fusion gearbox fault location method for wind turbines, the specific steps are as follows:
[0046] Step 1: Determine the application conditions of the fault location model according to the internal structure of the gearbox and the installation position and quantity of vibration sensors. Wind turbine gearboxes are composed of gears, bearings, shafts and corresponding accessories. Due to the difference in transmission power and manufacturers, the parameters of the internal components of the gearbox are different, so there are differences in the number of components and vibration characteristics for fault location. Different installation locations and installation quantities of vibration sensors will lead t...
PUM
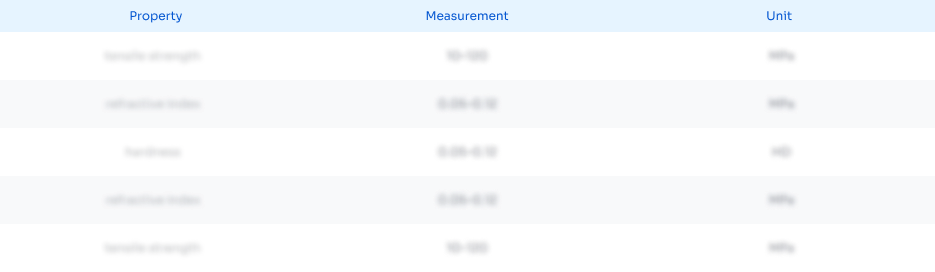
Abstract
Description
Claims
Application Information

- Generate Ideas
- Intellectual Property
- Life Sciences
- Materials
- Tech Scout
- Unparalleled Data Quality
- Higher Quality Content
- 60% Fewer Hallucinations
Browse by: Latest US Patents, China's latest patents, Technical Efficacy Thesaurus, Application Domain, Technology Topic, Popular Technical Reports.
© 2025 PatSnap. All rights reserved.Legal|Privacy policy|Modern Slavery Act Transparency Statement|Sitemap|About US| Contact US: help@patsnap.com