Preparation method of polybutadiene
A technology of polybutadiene and polymerization reaction, applied in the field of polymers, can solve the problems of low polybutadiene yield and low catalytic activity, etc.
- Summary
- Abstract
- Description
- Claims
- Application Information
AI Technical Summary
Problems solved by technology
Method used
Image
Examples
preparation example Construction
[0033] The embodiment of the invention discloses a preparation method of polybutadiene, specifically:
[0034] Polybutadiene is polymerized in an organic solvent under the action of a cocatalyst and a cobalt complex having the structure of formula (I) to obtain polybutadiene;
[0035]
[0036] Among them, R 1 and R 2 each independently selected from hydrogen or C1~C10 alkyl;
[0037] R 3 is hydrogen, halogen or C1~C10 alkyl;
[0038] X is halogen.
[0039] In the above polymerization reaction process, the cobalt complex catalyzes the polymerization of butadiene alone and has catalytic activity, but after adding a cocatalyst, the cobalt complex and the cocatalyst jointly catalyze the polymerization of butadiene, and the catalyst has a higher catalytic activity. active. The cocatalyst is preferably diethylsesquialuminum, triisobutylaluminum, triethylaluminum or methylalkoxyaluminum, more preferably diethylsesquialuminum. The molar ratio of aluminum in the cocatalyst to...
Embodiment 1
[0062] Weigh 5g (30mmol) of pyridine-2,6-dicarboxylic acid into a 50mL round-bottomed flask, add 30mL of thionyl chloride, reflux for 24h to form a homogeneous phase, and drain the excess thionyl chloride under reduced pressure to obtain a pale pink Pyridinedicarboxylic acid chloride was directly used in the next reaction.
[0063] Weigh 8.11g (60mmol) 2,4,6-trimethylaniline and 8.36g (60mmol) triethylamine and dissolve in 50ml CH 2 Cl 2 In, weigh 6.1g (30mmol) pyridinedicarboxylic acid chloride and dissolve in 20mL CH 2 Cl 2 In, pyridine dicarbonyl chloride / CH 2 Cl 2 Solution to substituted aniline / CH 2 Cl 2 Added dropwise in the middle, after reflux for 4 hours, use 100ml water and 100ml1.5M Na respectively 2 CO 3 The solution was washed, and the lower layer of CH was obtained with a separatory funnel 2 Cl 2 solution, adding MgSO 4 Dry overnight, filter and suck dry, then recrystallize with toluene, filter and dry to obtain the product (5b), the yield is 91%. The...
Embodiment 2
[0069] Weigh 5g (30mmol) of picidinedicarboxylic acid into a 50mL round-bottomed flask, add 30mL of thionyl chloride, reflux for 24h to form a homogeneous phase, and drain the excess thionyl chloride under reduced pressure to obtain pale pink pyridinedicarboxylic acid chloride, directly used in the next reaction.
[0070] Weigh 9.3g (60mmol) 4-chloro-2,6-dimethylaniline and 8.36ml (60mmol) triethylamine and dissolve in 50mL CH 2 Cl 2 In, weigh 6.1g (30mmol) pyridinedicarboxylic acid chloride and dissolve in 20mL CH 2 Cl 2 In, pyridine dicarbonyl chloride / CH 2 Cl 2 Solution to substituted aniline / CH 2 Cl 2 Added dropwise in the middle, after reflux for 4 hours, with 100mL water and 100mL1.5M Na 2 CO 3 The solution was washed, and the lower layer of CH was obtained with a separatory funnel 2 Cl 2 solution, adding MgSO 4 Dry overnight, filter and suck dry, then recrystallize with toluene, filter and dry to obtain the product (9b). Yield 83.5%. The product (9b) was an...
PUM
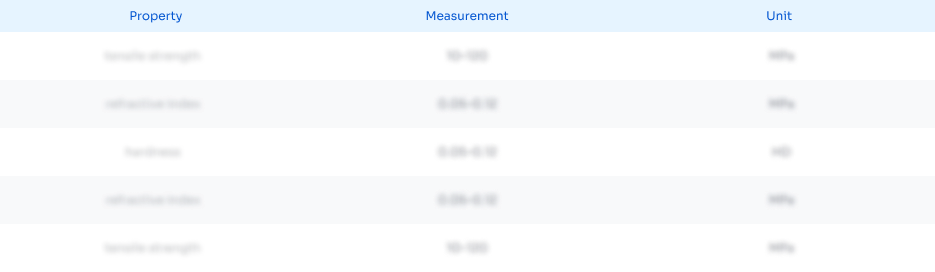
Abstract
Description
Claims
Application Information

- Generate Ideas
- Intellectual Property
- Life Sciences
- Materials
- Tech Scout
- Unparalleled Data Quality
- Higher Quality Content
- 60% Fewer Hallucinations
Browse by: Latest US Patents, China's latest patents, Technical Efficacy Thesaurus, Application Domain, Technology Topic, Popular Technical Reports.
© 2025 PatSnap. All rights reserved.Legal|Privacy policy|Modern Slavery Act Transparency Statement|Sitemap|About US| Contact US: help@patsnap.com