Comprehensive dust recovery method for ferroalloy electric furnace
A technology for collecting dust and iron alloys, applied in the direction of improving process efficiency, etc., can solve problems such as waste, low recovery rate, and large dust loss, and achieve the effect of ensuring normal stability and significant economic benefits
- Summary
- Abstract
- Description
- Claims
- Application Information
AI Technical Summary
Problems solved by technology
Method used
Examples
Embodiment 1
[0022] Example 1: The dust collection ash provided by a manganese alloy production enterprise in southern my country, the main components are: Mn: 27.00%, K: 10.01%, Fe: 3.02%, Cu: 0.03%, Pb: 6.50%, Zn: 1.37 %, Ge:660g / t, In:800g / t, Ga:40g / t.
[0023] Sampling 1000g, controlling the liquid-solid ratio 3:1, catalytic leaching at 80°C for 150min, filtering, washing, and drying to obtain 937g of the sample, the analysis of the solid composition is: Mn: 28.90%, K: 0.79%, Fe: 2.85%, Cu : 0.02%, Pb: 1.57%, Zn: 0.45%, Ga: 17g / t, Ge: 55g / t, In: 76g / t. The solution can effectively separate lead, zinc, gallium, germanium, indium, potassium and sodium. The solid phase can be dried and then returned to the electric furnace or directly prepared to produce electrolytic manganese.
Embodiment 2
[0024] Embodiment 2, the dust collection ash that a manganese alloy production enterprise in the north of my country provides, its main chemical composition is: Mn:33.50%, K:17.35%, Fe:5.24%, Cu:0.37%, Pb:3.82% , Zn: 4.05%, Ge: 1152g / t, In: 2175g / t, Ga: 89g / t.
[0025] Take a sample of 1000g, control the liquid-solid ratio to 3.5:1, add 50ppm of catalyst, the leaching temperature is 85°C, and the leaching time is 150min. After filtering and washing, dry to constant weight at 105°C, the amount of solid phase substance obtained is 890g, and its chemical composition is analyzed: Mn: 37.50%, K2.17%, Fe: 3.86%, Cu: 0.13%, Pb: 0.84%, Zn: 1.15%, Ge: 113g / t, In: 176g / t, Ga: 29g / t.
[0026] After the solid phase is dried, return to the electric furnace or directly prepare liquid to produce electrolytic manganese. Recovery of valuable elements from the solution has high value and significant economic benefits.
[0027] It has been verified by a small electric furnace that after remova...
Embodiment 3
[0029] Embodiment 3: the dust collection ash that a certain ferromolybdenum production enterprise in Shaanxi provides, its main component is: Mo:55.68%, K:9.97%, Fe:8.53%, Cu:0.45%, Pb:2.14%, Zn: 3.01%, Ge: 403g / t, In: 327g / t, Ga: 75g / t.
[0030] Sampling 1000g, liquid-solid ratio 3:1, add catalyst 35ppm, leave for 150min, temperature 90°C, after liquid-solid separation, weigh 948g of solid phase after drying, analyze its chemistry: Mo: 59.23%, K: 0.94% , Fe: 5.39%, Cu: 0.17%, Pb: 0.51%, Zn: 0.68%, Ge: 76g / t, In: 96g / t, Ga: 22g / t.
[0031] The solid phase returns to the electric furnace without hindrance.
PUM
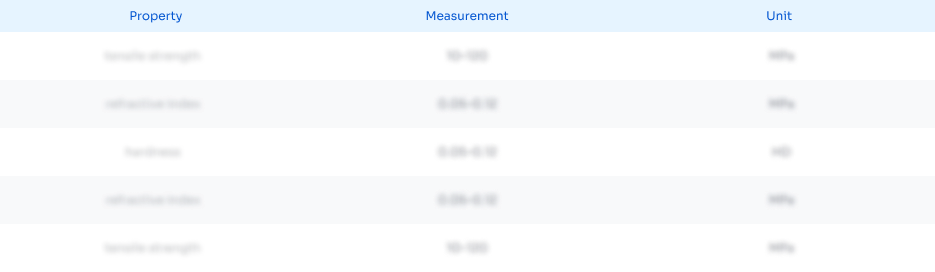
Abstract
Description
Claims
Application Information

- R&D
- Intellectual Property
- Life Sciences
- Materials
- Tech Scout
- Unparalleled Data Quality
- Higher Quality Content
- 60% Fewer Hallucinations
Browse by: Latest US Patents, China's latest patents, Technical Efficacy Thesaurus, Application Domain, Technology Topic, Popular Technical Reports.
© 2025 PatSnap. All rights reserved.Legal|Privacy policy|Modern Slavery Act Transparency Statement|Sitemap|About US| Contact US: help@patsnap.com