Method for preparing large-scale graphene in industrial large-scale reaction vessel
A reaction kettle, graphene technology, applied in graphene, nanotechnology, nanocarbon and other directions, can solve the problems of high impurity ion content, long production cycle and high cost, and achieve low impurity ion content, low cost and large output. Effect
- Summary
- Abstract
- Description
- Claims
- Application Information
AI Technical Summary
Problems solved by technology
Method used
Image
Examples
Embodiment 1
[0040] 1. Graphite mixed with concentrated sulfuric acid
[0041] First, 50.0g of commercial graphite powder (purity 98%) and 2L of 98% concentrated sulfuric acid are added to a 5L industrial large-scale reactor and stirred to make them evenly mixed, while using a circulating cooling device to keep the temperature in the reactor below 20 degrees Celsius;
[0042] 2. Add potassium permanganate
[0043] After mixing evenly, slowly (very slowly, the temperature will rise sharply during heating) add 250g potassium permanganate into the above reaction kettle, and at the same time stir the above solution with a mechanical stirrer at high speed, so that the potassium permanganate can fully mix with the above solution Contact; during the addition process, use external circulation cooling equipment to keep the temperature of the reaction solution in the kettle below 20 degrees Celsius; at this time, the solution turned from black to dark green; after the addition, the temperature of th...
Embodiment 2
[0054] 1. Graphite mixed with concentrated sulfuric acid
[0055] First, 100g of graphite powder recovered from waste batteries and 4L of 98% concentrated sulfuric acid are added to a 10L industrial large-scale reactor and stirred to make them evenly mixed. At the same time, a circulating cooling device is used to keep the temperature in the reactor below 20 degrees Celsius;
[0056] 2. Add potassium permanganate
[0057] After mixing evenly, slowly (very slowly, the temperature will rise sharply during heating) add 500g potassium permanganate into the above reaction kettle, and at the same time stir the above solution with a mechanical stirrer at high speed, so that the potassium permanganate can fully mix with the above solution Contact; during the addition process, use external circulation cooling equipment to keep the temperature of the reaction solution in the kettle below 20 degrees Celsius; at this time, the solution turned from black to dark green; after the addition, ...
Embodiment 3
[0067] 1. Graphite mixed with concentrated sulfuric acid
[0068] First, 500g of commercial graphite powder (purity 99.8%) and 20L of 98% concentrated sulfuric acid are added to a 50L industrial large-scale reactor and stirred to make them evenly mixed. At the same time, a circulating cooling device is used to keep the temperature in the reactor below 20 degrees Celsius;
[0069] 2. Add potassium permanganate
[0070] After mixing evenly, add 2500g potassium permanganate into the above reaction kettle slowly (very slowly, the temperature will rise sharply during the heating process), and at the same time stir the above solution with a mechanical stirrer at a high speed, so that the potassium permanganate can fully mix with the above solution. Contact; during the addition process, use external circulation cooling equipment to keep the temperature of the reaction solution in the kettle below 20 degrees Celsius; at this time, the solution turned from black to dark green; after th...
PUM
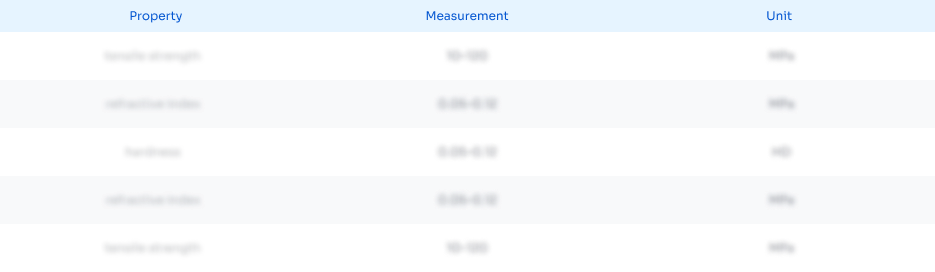
Abstract
Description
Claims
Application Information

- R&D
- Intellectual Property
- Life Sciences
- Materials
- Tech Scout
- Unparalleled Data Quality
- Higher Quality Content
- 60% Fewer Hallucinations
Browse by: Latest US Patents, China's latest patents, Technical Efficacy Thesaurus, Application Domain, Technology Topic, Popular Technical Reports.
© 2025 PatSnap. All rights reserved.Legal|Privacy policy|Modern Slavery Act Transparency Statement|Sitemap|About US| Contact US: help@patsnap.com