Method and device for improving room temperature plasticity of block amorphous alloy and structural member of block amorphous alloy
A technology of amorphous alloys and structural parts, applied in the field of advanced materials, can solve problems such as long time-consuming, complicated processing, and inability to adapt to shapes, etc., and achieve the effects of short processing time, simple process, and high rigidity
- Summary
- Abstract
- Description
- Claims
- Application Information
AI Technical Summary
Problems solved by technology
Method used
Image
Examples
Embodiment 1
[0043] Use the above-mentioned device to polish the surface of the Zr35Ti30Cu8.25Be26.75 amorphous alloy body with a size of 33.5mm×3mm×1.5mm rectangular cross-section beam and place it on a rigid backing plate. The boss of the center hole, the boss is arranged along the surface normal direction of the amorphous alloy body, and presses the surface, the diameter of the center hole of the boss is 2mm;
[0044] Pass a short pulse laser beam to the center hole of the boss, the pulse width of the laser beam is 11ns, and the maximum power density is 8GW / cm 2 , irradiate the surface of the amorphous alloy body to generate explosive plasma shock waves, and the shock wave acts on the amorphous alloy body, causing a small amount of high strain rate plastic deformation in the irradiated area, forming micro pits, and the plastic deformation will be constrained by the boss At the same time, it is also constrained by the surrounding undeformed area, so it is carried out under the state of t...
Embodiment 2
[0047] Use the above-mentioned device to polish the surface of an amorphous alloy body with a rectangular cross-section beam shape of 33.5mm×3mm×1.5mm and place it on a rigid backing plate. The amorphous alloy material is Zr41.2Ti13.8Cu12.5Ni10Be22.5. Place an inverted boss with a central hole on the amorphous alloy body, the boss is set along the surface normal of the amorphous alloy body, and press the surface, the diameter of the center hole of the boss is 2mm;
[0048] Pass a short pulse laser beam to the center hole of the boss, the pulse width of the laser beam is 11ns, and the maximum power density is 8GW / cm 2 , irradiate the surface of the amorphous alloy body to generate explosive plasma shock waves, and the shock wave acts on the amorphous alloy body, causing a small amount of high strain rate plastic deformation in the irradiated area, forming micro pits, and the plastic deformation will be constrained by the boss At the same time, it is also constrained by the surr...
PUM
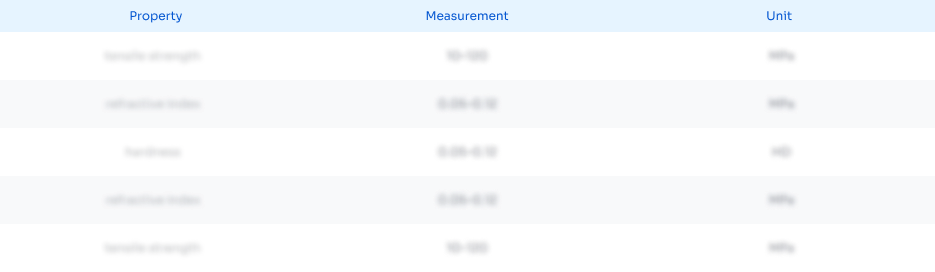
Abstract
Description
Claims
Application Information

- R&D
- Intellectual Property
- Life Sciences
- Materials
- Tech Scout
- Unparalleled Data Quality
- Higher Quality Content
- 60% Fewer Hallucinations
Browse by: Latest US Patents, China's latest patents, Technical Efficacy Thesaurus, Application Domain, Technology Topic, Popular Technical Reports.
© 2025 PatSnap. All rights reserved.Legal|Privacy policy|Modern Slavery Act Transparency Statement|Sitemap|About US| Contact US: help@patsnap.com