Method for comprehensively utilizing vanadium titano-magnetite by melting and separating through reduction-fuel smelting furnace of rotary hearth furnace
A vanadium-titanium magnetite and gas-fired smelting furnace technology, applied in the direction of rotary drum furnaces, furnaces, furnace types, etc., can solve the problems of high carbon content, poor slag fluidity, high energy consumption, etc., to achieve low carbon content, lighten Effect of smelting burden and enhanced degassing effect
- Summary
- Abstract
- Description
- Claims
- Application Information
AI Technical Summary
Problems solved by technology
Method used
Image
Examples
Embodiment 1
[0047] Composition of vanadium-titanium magnetite: TFe 59.28%, TiO 2 9.14%, V 2 o 5 0.47%. More than 100 mesh accounted for 90%, using anthracite below 1mm, of which 75.34% fixed carbon, 10.94% ash, 12.5% volatile matter, 0.45% total sulfur. The material ratio is: vanadium-titanium ore: pulverized coal: binder = 100:24:6. After mixing evenly, use a double-roller briquetting machine to make pellets. After drying, the pellets enter the bottom of the rotary hearth furnace through a distribution machine. Double-layer distribution, the thickness is about 24mm. The reduction temperature in the furnace is between 1200 and 1350°C, and the holding time at 1350°C is about 17 minutes, and the whole reduction process takes 39 minutes. The metallization rate after pre-reduction in the rotary hearth furnace is >88%, and the hot cans enter the gas melting furnace. The temperature of the gas furnace is 1450~1620 ° C, and the melting time is 60 minutes. After smelting, the titanium slag...
Embodiment 2
[0049] Vanadium-titanium magnetite composition: TFe 54.45%, TiO 2 16.24%, V 2 o 5 1.02%. More than 200 mesh accounted for 40%, using anthracite below 1mm, of which 75.34% fixed carbon, 10.94% ash, 12.5% volatile matter, 0.45% total sulfur. The material ratio is: vanadium-titanium ore: pulverized coal: binder = 100:24:6. After mixing evenly, use a double-roller briquetting machine to make pellets. After drying, the pellets enter the bottom of the rotary hearth furnace through a distribution machine. Double-layer distribution, the thickness is about 24mm. The reduction temperature in the furnace is between 1150 and 1350°C, and the holding time at 1350°C is about 17 minutes, and the whole reduction process takes 39 minutes. The metallization rate after pre-reduction in the rotary hearth furnace is >90%, and the hot cans enter the gas melting furnace. The temperature of the gas furnace is 1450~1600 ° C, and the melting time is 60 minutes. After smelting, the titanium slag a...
PUM
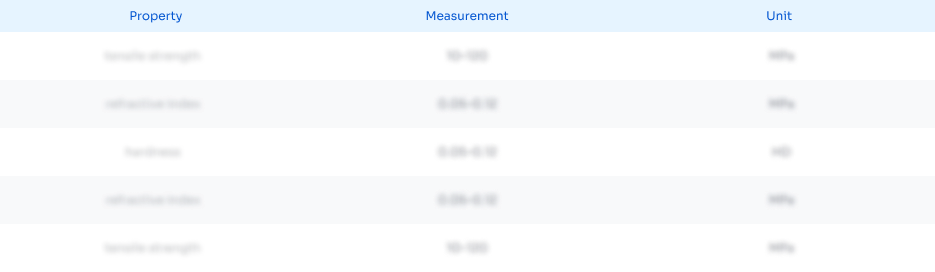
Abstract
Description
Claims
Application Information

- R&D
- Intellectual Property
- Life Sciences
- Materials
- Tech Scout
- Unparalleled Data Quality
- Higher Quality Content
- 60% Fewer Hallucinations
Browse by: Latest US Patents, China's latest patents, Technical Efficacy Thesaurus, Application Domain, Technology Topic, Popular Technical Reports.
© 2025 PatSnap. All rights reserved.Legal|Privacy policy|Modern Slavery Act Transparency Statement|Sitemap|About US| Contact US: help@patsnap.com