Washing and separation method of nitrobenzene
A separation method and technology of nitrobenzene, which are applied in chemical instruments and methods, preparation of organic compounds, organic chemistry, etc., can solve the problems of large water consumption, large floor space, and large number of equipment, so as to reduce equipment occupation. land area, reducing alkali consumption, good mixing effect
- Summary
- Abstract
- Description
- Claims
- Application Information
AI Technical Summary
Problems solved by technology
Method used
Image
Examples
Embodiment 1
[0019] Nitrobenzene washing and separation method, the device used mainly includes a nitration separator (1), a coalescence separator (2), a centrifugal extractor (5) for neutralization and a centrifugal extractor for water washing machine (8), a crude nitrobenzene delivery pump (3), a lye delivery pump (4), and a water delivery pump (7).
Embodiment 2
[0023] The structure of the device is roughly the same as in Example 1, except that the coalescing separator (2) uses plate-type packing. The volume ratio of nitrobenzene and lye into the neutralization centrifugal extractor (5) is 5:1, and the ratio of nitrobenzene to water into the washing centrifugal extractor (8) is 1:1.
Embodiment 3
[0025] The structure of the device is roughly the same as that of Example 1, except that the coalescing separator (2) uses a combination of plate type and fiber filter element packing. The volume ratio of nitrobenzene and lye in the neutralization centrifugal extractor (5) is 3:1, and the ratio of nitrobenzene and water in the washing centrifugal extractor (8) is 3:1.
[0026] The results of sodium ion content and phenate content in the crude nitrobenzene before and after washing in the above examples are shown in Table 1 below.
[0027] Table 1 Sodium salt content and phenate content in crude nitrobenzene
[0028]
PUM
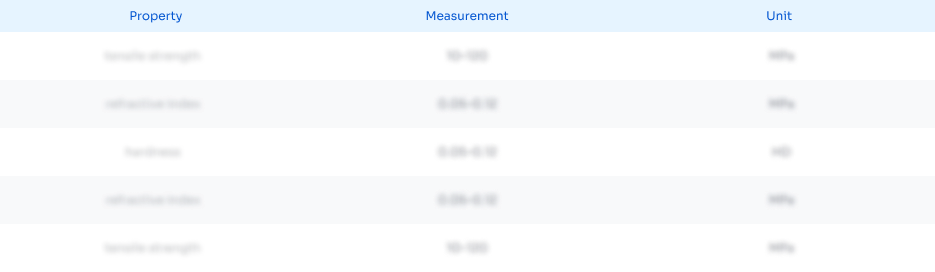
Abstract
Description
Claims
Application Information

- R&D
- Intellectual Property
- Life Sciences
- Materials
- Tech Scout
- Unparalleled Data Quality
- Higher Quality Content
- 60% Fewer Hallucinations
Browse by: Latest US Patents, China's latest patents, Technical Efficacy Thesaurus, Application Domain, Technology Topic, Popular Technical Reports.
© 2025 PatSnap. All rights reserved.Legal|Privacy policy|Modern Slavery Act Transparency Statement|Sitemap|About US| Contact US: help@patsnap.com