Process for preparing butadiene through oxidative dehydrogenation of butene
A technology for oxidative dehydrogenation and butadiene, which is applied in the chemical industry, sustainable manufacturing/processing, organic chemistry, etc., can solve the problems of easy crushing of catalysts, large total steam consumption, loss and consumption, and achieve short flow channels, The effect of large production capacity and low resistance
- Summary
- Abstract
- Description
- Claims
- Application Information
AI Technical Summary
Problems solved by technology
Method used
Image
Examples
Embodiment 1
[0022] The oxidative dehydrogenation process of the butadiene plant with an annual output of 100,000 tons adopts the three-stage oxidation reaction process of the present invention. The adiabatic fixed-bed reactors are 3 units in one group, steam is added to the first stage, water is added to the second and third stages, and each stage is reacted. The percentage of butene added is: 40:30:30.
[0023] Add 0.7MPa.G medium pressure steam in the first stage: 50 tons / hour.
[0024] The amount of water added in the second stage: 0.5 tons / hour.
[0025] The amount of water added in the third stage: 0.5 tons / hour.
[0026] The third stage by-product 0.7MPa.G medium pressure steam volume: 33.7 tons / hour.
[0027] The third stage by-product 0.3MPa.G low pressure steam volume: 2.3 tons / hour.
[0028] Total water to olefin ratio: 7.2:1.
[0029] Medium-pressure steam consumption: 16.3 tons / hour (the amount of medium-pressure steam added in the first stage minus the amount of by-produc...
Embodiment 2
[0035] The oxidative dehydrogenation process of the butadiene plant with an annual output of 100,000 tons adopts the three-stage oxidation reaction process of the present invention. Join percentage: 45:30:25.
[0036] Add 0.7MPa.G medium pressure steam in the first stage: 54 tons / hour.
[0037] The amount of water added in the second stage: 0.7 tons / hour.
[0038] The amount of water added in the third stage: 0.5 tons / hour.
[0039] The third stage by-product 0.7MPa.G medium pressure steam volume: 33.3 tons / hour.
[0040] The third stage by-product 0.3MPa.G low pressure steam volume: 2.3 tons / hour.
[0041] Total water-ene ratio: 7.5:1.
[0042] Medium-pressure steam consumption: 20.7 tons / hour (the amount of medium-pressure steam added in the first stage minus the amount of by-product medium-pressure steam in the third stage).
[0043] Medium-pressure steam consumption per ton of butadiene: 1.656 tons / ton of butadiene.
[0044] When adopting two-stage adiabatic fixed-be...
Embodiment 3
[0048] The oxidative dehydrogenation process of the butadiene plant with an annual output of 100,000 tons adopts the three-stage oxidation reaction process of the present invention. The joining percentage is: 45:35:20.
[0049] Add 0.7MPa.G medium pressure steam in the first stage: 54 tons / hour.
[0050] The amount of water added in the second stage: 0.1 t / h.
[0051] The amount of water added in the third stage: 1.2 tons / hour.
[0052] The third stage by-product 0.7MPa.G medium pressure steam volume: 36.1 tons / hour.
[0053] The third stage by-product 0.3MPa.G low pressure steam volume: 2.3 tons / hour.
[0054] Total water-ene ratio: 7.5:1.
[0055] Medium-pressure steam consumption: 17.9 tons / hour (the amount of medium-pressure steam added in the first stage minus the amount of by-product medium-pressure steam in the third stage).
[0056] Medium-pressure steam consumption per ton of butadiene: 1.432 tons / ton of butadiene.
[0057] When adopting two-stage adiabatic fixe...
PUM
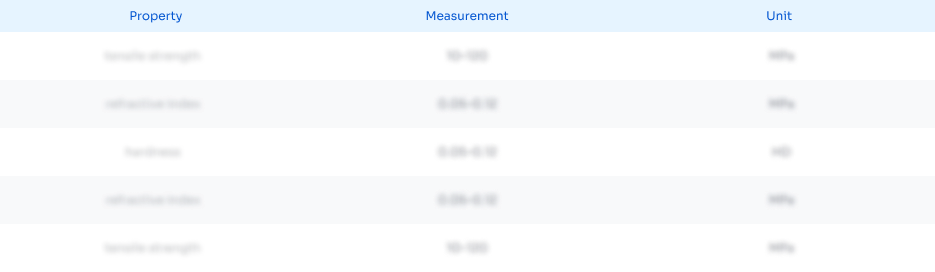
Abstract
Description
Claims
Application Information

- R&D
- Intellectual Property
- Life Sciences
- Materials
- Tech Scout
- Unparalleled Data Quality
- Higher Quality Content
- 60% Fewer Hallucinations
Browse by: Latest US Patents, China's latest patents, Technical Efficacy Thesaurus, Application Domain, Technology Topic, Popular Technical Reports.
© 2025 PatSnap. All rights reserved.Legal|Privacy policy|Modern Slavery Act Transparency Statement|Sitemap|About US| Contact US: help@patsnap.com