Production process of temperature adjusting raschel blanket
A production process and blanket technology, which is applied in the field of temperature-adjusted Raschel blanket production process, can solve the problems of poor fabric feel and comfort, good fabric feel and comfort, and inability to adjust temperature, so as to achieve soft feel and good fabric style , low-cost effect
- Summary
- Abstract
- Description
- Claims
- Application Information
AI Technical Summary
Problems solved by technology
Method used
Image
Examples
Embodiment 1
[0028] A production process for a temperature-regulating Raschel blanket, comprising the steps of:
[0029] Step a) Weaving: Knit the temperature-adjusted yarn on a double-needle-bed Raschel warp knitting machine into gray fabric with three layers of spacer weave. The knitting process is: the bar L1 and L6 uses 100D / 50F polyester filament to weave weft insertion, bar L2 and L5 use 100D / 50F polyester filament to weave and knit chain, and bar L3 wears 200D temperature-adjusting yarn every other space to weave warp flat on double needle bed. Bar L4 is vacant, and after weaving is completed, the finished gray cloth is inspected; the temperature-regulating yarn is a blended yarn of outlast fiber and expanded acrylic fiber, wherein the mass fraction of outlast fiber is 70%;
[0030] The temperature-adjusting yarn is a blended yarn of outlast fiber and expanded acrylic fiber, and the outlast fiber and expanded acrylic fiber can be purchased from the known market, and the double-needl...
Embodiment 2
[0039] Step a) Weaving: Knit the temperature-adjusted yarn on a double-needle-bed Raschel warp knitting machine into gray fabric with three layers of spacer weave. The knitting process is: the bar L1 and L6 uses 150D / 75F polyester filament to weave weft insertion, bar L2 and L5 use 150D / 75F polyester filament to weave and knit chain, and bar L3 wears 250D temperature-adjusting yarn at intervals to weave warp and flat on double needle beds. Bar L4 is vacant, and after weaving is completed, the finished gray cloth is inspected; the temperature-regulating yarn is a blended yarn of outlast fiber and expanded acrylic fiber, wherein the mass fraction of outlast fiber is 80%;
[0040] Step b) Printing: Print the gray cloth that passed the blank inspection, the printing speed is 12m / min, the pressure of the printing roller is 4Kg, the printing paste contains 0.7% o.w.f of 1227 leveling agent and 40% of the original paste, and the balance is Water, the pH value of the printing paste is...
Embodiment 3
[0048] Step a) Weaving: Knit the temperature-adjusted yarn on a double-needle-bed Raschel warp knitting machine into gray fabric with three layers of spacer weave. The knitting process is: the bar L1 and L6 uses 150D / 75F polyester filament to weave weft insertion, bar L2 and L5 use 150D / 75F polyester filament to weave and knit chain, bar L3 wears 300D temperature-adjusting yarn at intervals and weaves warp flat on double needle bed, Bar L4 is vacant, and after weaving is completed, the finished gray cloth is inspected; the temperature-regulating yarn is a blended yarn of outlast fiber and expanded acrylic fiber, wherein the mass fraction of outlast fiber is 85%;
[0049] Step b) Printing: Print the gray cloth that has passed the blank inspection, the printing speed is 13m / min, the pressure of the printing roller is 5Kg, the printing paste contains 0.8% o.w.f of 1227 leveling agent and 40% of the original paste, and the balance is water , the pH value of printing paste is 5;
...
PUM
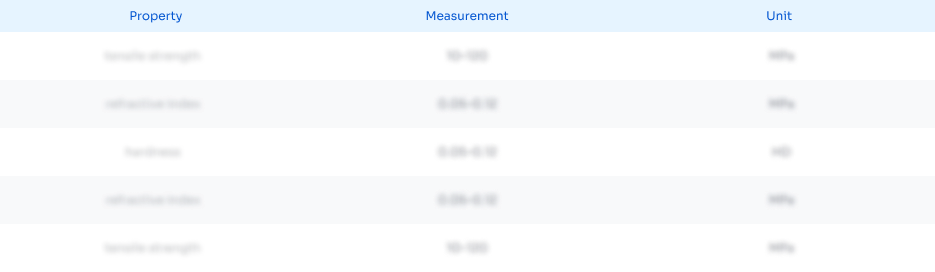
Abstract
Description
Claims
Application Information

- Generate Ideas
- Intellectual Property
- Life Sciences
- Materials
- Tech Scout
- Unparalleled Data Quality
- Higher Quality Content
- 60% Fewer Hallucinations
Browse by: Latest US Patents, China's latest patents, Technical Efficacy Thesaurus, Application Domain, Technology Topic, Popular Technical Reports.
© 2025 PatSnap. All rights reserved.Legal|Privacy policy|Modern Slavery Act Transparency Statement|Sitemap|About US| Contact US: help@patsnap.com