Preparation method for oxide fiber toughened silicon dioxide ceramic-based composite material gap interface
A composite material and silica technology, which is applied in the field of preparation of oxide fiber toughened silica ceramic matrix composite material gap type interface, can solve the problems affecting the mechanical properties of fibers, glass fiber and quartz fiber damage, etc., to achieve fiber Low degree of damage, low preparation temperature, and the effect of improving toughness
- Summary
- Abstract
- Description
- Claims
- Application Information
AI Technical Summary
Problems solved by technology
Method used
Examples
Embodiment 1
[0025] (1) First, add an appropriate amount of C 60 Dissolve in toluene until reaching a saturated solution;
[0026] (2) The oxide fiber is selected as a three-dimensional braided quartz fiber prefabricated part. Put it into a saturated solution, fully impregnate it, let it stand for 5 minutes, then take out the fiber preform and place it in an air atmosphere at 30°C until the toluene is completely volatilized;
[0027] (3) Put the quartz fiber prefabricated part in the saturated solution again, after being completely impregnated, take it out after 1 minute, place it in an air atmosphere at 30°C until the toluene is completely volatilized, repeat this cycle 3 times, at this time, the quartz fiber prefabricated part The surface is covered with a large amount of C 60 ;
[0028] (4) Put the quartz fiber preform into silica sol with a concentration of 5% for impregnation, pump the air pressure in the impregnation tank to negative pressure, and use the negative pressure to suck...
Embodiment 2
[0032] (1) First, add an appropriate amount of C 60 Dissolve in 2L xylene until reaching a saturated solution;
[0033] (2) The oxide fiber is selected as a two-dimensional braided alumina fiber prefabricated part, which is placed in a saturated solution, fully impregnated, and left to stand for 8 minutes, then the fiber prefabricated part is taken out, and placed in an air atmosphere at 30 °C to wait Xylene is completely volatile;
[0034] (3) Place the alumina fiber prefabricated part in the xylene solution. After being completely immersed, take it out after 2 minutes, and place it in an air atmosphere at 35°C until the xylene is completely volatilized. Repeat this cycle 3 times. At this time, the alumina fiber The surface of the fiber preform is covered with a large amount of C 60 ;
[0035] (4) Put the alumina fiber preform into the silica sol with a concentration of 10% for impregnation, pump the air pressure in the impregnation tank to negative pressure, and use the n...
PUM
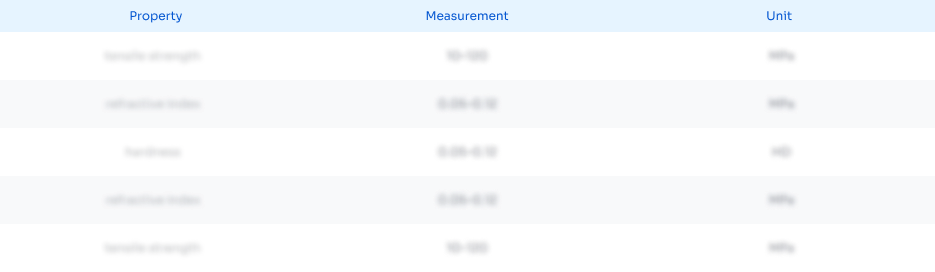
Abstract
Description
Claims
Application Information

- R&D Engineer
- R&D Manager
- IP Professional
- Industry Leading Data Capabilities
- Powerful AI technology
- Patent DNA Extraction
Browse by: Latest US Patents, China's latest patents, Technical Efficacy Thesaurus, Application Domain, Technology Topic, Popular Technical Reports.
© 2024 PatSnap. All rights reserved.Legal|Privacy policy|Modern Slavery Act Transparency Statement|Sitemap|About US| Contact US: help@patsnap.com