Vacuum brazing method of gas burner of combustion chamber of gas turbine
A technology of gas nozzle and brazing method, applied in welding equipment, metal processing equipment, manufacturing tools, etc., can solve the problems of affecting the production cycle and quality of gas turbines, poor welding quality, large welding deformation, etc., to reduce the probability of repair, welding The effect of good quality and easy weld formation
- Summary
- Abstract
- Description
- Claims
- Application Information
AI Technical Summary
Problems solved by technology
Method used
Image
Examples
specific Embodiment approach 1
[0014] Specific implementation mode one: combine figure 1 and figure 2 Describe this embodiment, the concrete steps of a kind of gas turbine combustor gas nozzle vacuum brazing method of this embodiment are:
[0015] Step 1. Clean the surfaces of the components of the gas nozzle to be welded, the workbench and the surface of the tooling;
[0016] Step 2, one-time assembly and welding: assemble and spot-weld some parts cleaned in step 1, first assemble the spout 9-2 and the bellows 9-1 and spot-weld to form the extruder 9; then assemble the second pressing part 8 Spot welding with the cup-shaped part 7 to form a cup-shaped assembly A; then assembling the cyclone 3 and the cone 1 and spot-welding and assembling the cyclone 3 and the ring sleeve 5 and spot-welding to form the cyclone assembly B; The extruder 9, the cup assembly A and the cyclone assembly B all ensure that the assembly gap is less than 0.10mm during the assembly process;
[0017] Step 3, one-time coating of br...
specific Embodiment approach 2
[0032] Specific embodiment two: the difference between this embodiment and specific embodiment one is: the brazing filler metal in step three is BNi73CrSiB-40Ni-S brazing filler metal. With such setting, the performance is reliable and meets the actual needs. Others are the same as in the first embodiment.
specific Embodiment approach 3
[0033] Embodiment 3: The difference between this embodiment and Embodiment 1 or 2 is that the solder in step 6 is BNi73CrSiB-40Ni-S solder. With such setting, the performance is reliable and meets the actual needs. Others are the same as in the first or second embodiment.
PUM
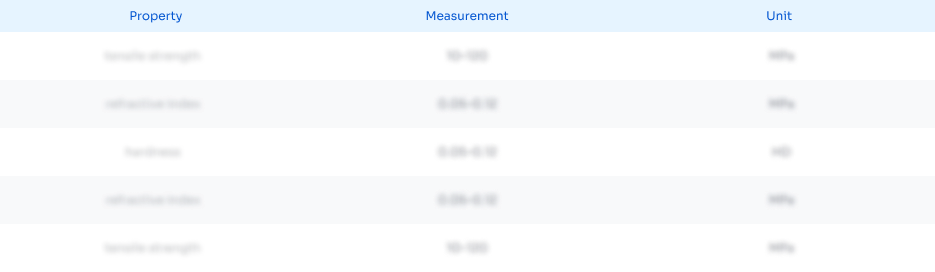
Abstract
Description
Claims
Application Information

- R&D
- Intellectual Property
- Life Sciences
- Materials
- Tech Scout
- Unparalleled Data Quality
- Higher Quality Content
- 60% Fewer Hallucinations
Browse by: Latest US Patents, China's latest patents, Technical Efficacy Thesaurus, Application Domain, Technology Topic, Popular Technical Reports.
© 2025 PatSnap. All rights reserved.Legal|Privacy policy|Modern Slavery Act Transparency Statement|Sitemap|About US| Contact US: help@patsnap.com