Preparation method of high-quality 6061 aluminium alloy forging for semiconductor equipment
A semiconductor and aluminum alloy technology, which is applied in the field of non-ferrous metal forging processing, can solve the problems of the uniformity of alloy structure and grain size being not strict, it is difficult to meet the use requirements of semiconductor equipment, and it is difficult to meet the use requirements. Good tissue uniformity, significant economic and social benefits, and high product added value
- Summary
- Abstract
- Description
- Claims
- Application Information
AI Technical Summary
Problems solved by technology
Method used
Image
Examples
Embodiment 1
[0022] According to the 6061 aluminum alloy, the common semi-continuous casting casting process is adopted to obtain the billet with a size of Φ300×760mm, and the billet is homogenized and heat-treated in an air resistance furnace with a cyclone. The heat treatment system is 560°C×24h+580°C×24h , air cooling after heat treatment. The heat-treated billet is machined to a size of Φ275×740mm, and the machined billet is placed in an air resistance furnace for heating and heat preservation before forging at 480°C×225min. The billet is forged in two fires, and the forging is carried out on a 1600t hydraulic press. The first fire adopts the forging process of two upsetting and two drawing, and the specific deformation process is as follows (unit, mm):
[0023]
[0024]
[0025] After the first fire forging, the forging is returned to the furnace for heat preservation. The heat preservation system is 480℃×50min. After heat preservation, the second fire forging is carried out. Th...
Embodiment 2
[0031] According to the 6061 aluminum alloy, the ordinary semi-continuous casting casting process is adopted to obtain a billet with a size of Φ260×750mm, and the billet is subjected to homogenization heat treatment in an air resistance furnace with a cyclone, and the heat treatment system is 560°C×24h+580°C×24h , air cooling after heat treatment. The heat-treated billet is machined to a size of Φ245×730mm. The machined billet is placed in an air resistance furnace for heating and heat preservation before forging at 480°C×184min. The billet is forged in two fires, and the forging is carried out on a 1600t hydraulic press. The first fire adopts the forging process of two upsetting and two drawing, and the specific deformation process is as follows (unit, mm):
[0032]
[0033]
[0034]
[0035] Due to the relatively large height and diameter of the billet, double drums appear during the upsetting process, and corresponding straightening treatment is carried out in the ...
Embodiment 3
[0042] According to the 6061 aluminum alloy, the ordinary semi-continuous casting casting process is adopted to obtain a billet with a size of Φ200×540mm, and the billet is homogenized and heat-treated in an air resistance furnace with a cyclone. The heat treatment system is 560°C×24h+580°C×24h , air cooling after heat treatment. The heat-treated blank is machined to a size of Φ180×520mm, and the machined blank is placed in an air resistance furnace for heating and heat preservation before forging at 480°C×150min. Forging is carried out on an 800t hydraulic press.
[0043] The specific deformation process is as follows (unit, mm):
[0044]
[0045]
[0046]
[0047]After forging, the forging is subjected to solution aging treatment. The solution process is 530°C×140min, water quenching after solution, and then 4% pre-compression treatment on the press, followed by artificial aging treatment at 170°C×18h.
[0048] The high and low magnification inspection of the forg...
PUM
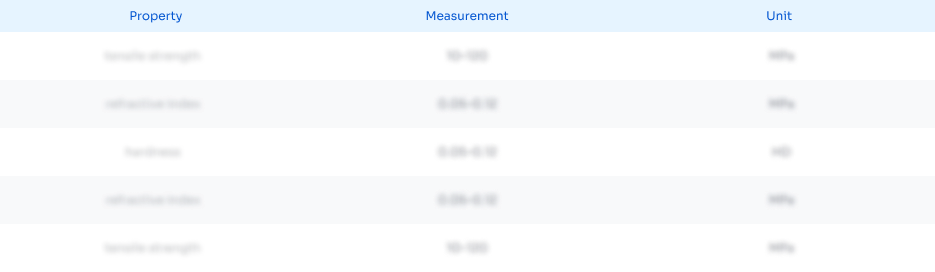
Abstract
Description
Claims
Application Information

- R&D
- Intellectual Property
- Life Sciences
- Materials
- Tech Scout
- Unparalleled Data Quality
- Higher Quality Content
- 60% Fewer Hallucinations
Browse by: Latest US Patents, China's latest patents, Technical Efficacy Thesaurus, Application Domain, Technology Topic, Popular Technical Reports.
© 2025 PatSnap. All rights reserved.Legal|Privacy policy|Modern Slavery Act Transparency Statement|Sitemap|About US| Contact US: help@patsnap.com