Method for producing high-safety caramel color through twice catalytic reaction
A secondary catalysis, high-safety technology, applied in chemical instruments and methods, azo dyes, organic dyes, etc., can solve the problem of high residues of 4-methylimidazole, large amount of reaction catalyst, and high residues of 3-chloropropanol and other problems, to achieve the effect of improving market competitiveness, saving catalyst dosage, and good coloring performance
- Summary
- Abstract
- Description
- Claims
- Application Information
AI Technical Summary
Problems solved by technology
Method used
Image
Examples
Embodiment 1
[0034] Such as figure 1 As shown, 1 ton of rice is crushed, and the rice crushing fineness is 100 mesh, and then the high-temperature-resistant amylase produced by Novozymes China Biological Co., Ltd. is used, and the optimum temperature is 95-105 degrees, and 1000 grams of crushed rice are added. and spray liquefaction at 103°C, add 900 grams of glucoamylase to the liquefied rice, and saccharify at 58°C for 16 hours. degree or degree of saccharification, the reducing sugar in the saccharification liquid is all counted as glucose, and the percentage of the dry matter is called DE value) ≥ 95% to stop saccharification, and use a plate and frame filter press to filter the saccharified glucose liquid until it is clear Transparent; the filtered solution is concentrated to 70% of the glucose solution on a dry basis through a three-effect concentration equipment, and the first catalytic reaction is performed. Calculated based on the mass ratio to the dry basis, 40% of the catalyst d...
Embodiment 2
[0038]Grind 1 ton of rice with a fineness of 100 meshes, then add 1,000 grams of high-temperature-resistant amylase to the crushed rice, spray and liquefy it at 105°C, and add 900 grams of glucoamylase to the liquefied rice , saccharified at 59°C for 16 hours, when the DE value (the DE value used in industry, also known as glucose value, indicates the degree of hydrolysis or saccharification of starch, all reducing sugars in the saccharification solution are calculated as glucose, the percentage of dry matter called DE value) ≥ 95% to stop saccharification, use plate and frame filter press to filter the saccharified glucose liquid until it is clear and transparent; use the three-effect concentration equipment to concentrate the glucose solution to 72% on a dry basis , carry out the first catalytic reaction, calculated by mass percentage, according to a catalytic reaction, 40% of the catalyst dosage is used to add the catalyst, and then the reaction is carried out by pressurizin...
Embodiment 3
[0040] Grind 1 ton of rice with a fineness of 100 meshes, then add 1,000 grams of high-temperature-resistant amylase to the crushed rice, spray and liquefy it at 107°C, and add 900 grams of glucoamylase to the liquefied rice , saccharified at 60°C for 16 hours, when the DE value (the DE value used in industry, also known as the glucose value, indicates the degree of hydrolysis or saccharification of starch, all the reducing sugars in the saccharification solution are calculated as glucose, the percentage of dry matter The saccharification is terminated after the DE value) ≥ 95%, and the saccharified glucose liquid is filtered with a plate and frame filter press until it is clear and transparent; the filtered solution is concentrated to 74% on a dry basis through a three-effect concentration equipment , carry out the first catalytic reaction, calculated by mass percentage, according to a catalytic reaction, 40% of the catalyst dosage is used to add the catalyst, and then the rea...
PUM
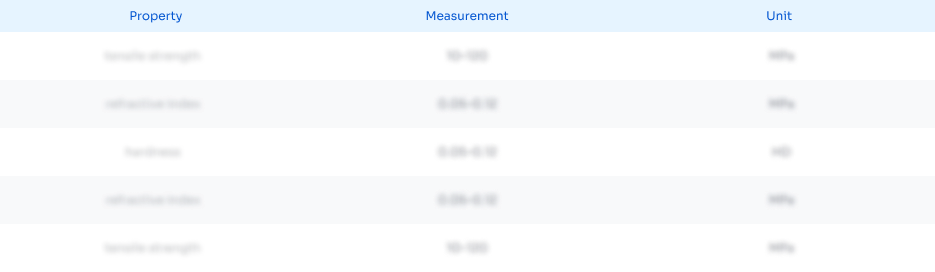
Abstract
Description
Claims
Application Information

- R&D
- Intellectual Property
- Life Sciences
- Materials
- Tech Scout
- Unparalleled Data Quality
- Higher Quality Content
- 60% Fewer Hallucinations
Browse by: Latest US Patents, China's latest patents, Technical Efficacy Thesaurus, Application Domain, Technology Topic, Popular Technical Reports.
© 2025 PatSnap. All rights reserved.Legal|Privacy policy|Modern Slavery Act Transparency Statement|Sitemap|About US| Contact US: help@patsnap.com