Efficient glass polishing powder and preparation method thereof
A technology of polishing powder and glass, which is applied in the direction of polishing compositions containing abrasives, etc. It can solve the problems of poor dispersion stability of polishing powder and low polishing efficiency, and achieve stable polishing effect, good dispersion stability and strong suspension
- Summary
- Abstract
- Description
- Claims
- Application Information
AI Technical Summary
Problems solved by technology
Method used
Examples
Embodiment 1
[0022] 1. Preparation method:
[0023] Weigh 5 kg of white mixed lanthanum cerium carbonate (rare earth oxide content 45%wt), add it to 5 kg of water, stir evenly at room temperature, and make a suspension.
[0024] Add 450 grams of manganese nitrate to the suspension, stir well, and make a mixed suspension containing manganese, lanthanum and cerium carbonate. Under the condition of stirring, adjust the pH to 10 with sodium hydroxide, then let it stand for precipitation, pour off the liquid, dry the solid in an oven at 120°C, and break it.
[0025] The dried and crushed solid powder was calcined at 960° C. for 12 hours to obtain dark red lanthanum cerium oxide polishing powder.
Embodiment 2
[0029] 1. Preparation method:
[0030] Weigh 5 kg of white mixed lanthanum cerium carbonate (rare earth oxide content 45%wt), add it to 5 kg of water, stir evenly at room temperature, and make a suspension.
[0031] Add 15 grams of manganese nitrate to the suspension and stir well to make a mixed suspension containing manganese, lanthanum and cerium carbonate. Under the condition of stirring, adjust the pH to 10 with sodium hydroxide, then let it stand for precipitation, pour off the liquid, dry the solid in an oven at 120°C, and break it.
[0032] The dried and crushed solid powder was calcined at 960° C. for 12 hours to obtain dark red lanthanum cerium oxide polishing powder.
[0033] 2. Application examples:
[0034] After the dark red lanthanum cerium oxide polishing powder was uniformly dispersed in water at a ratio of 1:6, it was polished and tested on a Logitech CDP single-side polishing machine. Down pressure: 1psi, the rotation speed of the lower plate and the carr...
Embodiment 3
[0036] 1. Preparation method:
[0037] Weigh 5 kg of white mixed lanthanum cerium carbonate (rare earth oxide content 45%wt), add it to 5 kg of water, stir evenly at room temperature, and make a suspension.
[0038] Add 45 grams of ferric nitrate to the suspension, stir well, and make a mixed suspension containing manganese, lanthanum and cerium carbonate. Under the condition of stirring, adjust the pH to 10 with sodium hydroxide, then let it stand for precipitation, pour off the liquid, dry the solid in an oven at 120°C, and break it.
[0039] The dried and crushed solid powder was calcined at 920° C. for 12 hours to obtain milky yellow lanthanum cerium oxide polishing powder.
[0040] 2. Application examples:
[0041] After the milky yellow lanthanum cerium oxide polishing powder was uniformly dispersed in water at a ratio of 1:6, it was polished and tested on a Logitech CDP single-side polishing machine. Down pressure: 1psi, rotation speed of the bottom plate and carrier...
PUM
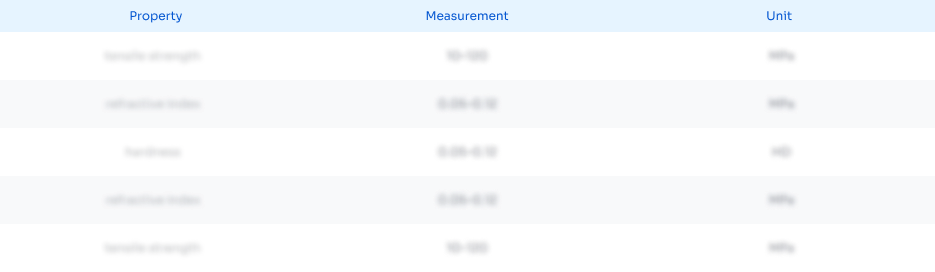
Abstract
Description
Claims
Application Information

- R&D
- Intellectual Property
- Life Sciences
- Materials
- Tech Scout
- Unparalleled Data Quality
- Higher Quality Content
- 60% Fewer Hallucinations
Browse by: Latest US Patents, China's latest patents, Technical Efficacy Thesaurus, Application Domain, Technology Topic, Popular Technical Reports.
© 2025 PatSnap. All rights reserved.Legal|Privacy policy|Modern Slavery Act Transparency Statement|Sitemap|About US| Contact US: help@patsnap.com