Method for connecting semi-solid materials into whole
A semi-solid slurry and semi-solid technology, applied in chemical instruments and methods, welding equipment, lamination, etc., can solve problems such as difficulty in obtaining comprehensive performance of joints
- Summary
- Abstract
- Description
- Claims
- Application Information
AI Technical Summary
Problems solved by technology
Method used
Image
Examples
specific Embodiment approach 1
[0035] Specific implementation mode 1: In this implementation mode, the semi-solid material connection and forming integration method is carried out according to the following steps:
[0036] 1. Prepare two or more pre-connected materials into semi-solid blanks or semi-solid slurries respectively, wherein the type of pre-connected materials prepared into semi-solid blanks is greater than or equal to the type of pre-connected materials prepared into semi-solid slurries type;
[0037] 2. If all pre-connected materials are prepared into semi-solid blanks in step 1, the semi-solid blanks of pre-connected materials prepared in step 1 are heated to a predetermined temperature range, and then the heated semi-solid blanks are placed in the mold cavity Or put it under the roll for thixotropic forming. After die forging or rolling is completed, take out the connected and formed parts to complete the integrated process of semi-solid connection and forming of the required parts;
[0038]...
specific Embodiment approach 2
[0042] Embodiment 2: This embodiment differs from Embodiment 1 in that the pre-connected material in step 1 is a metal material or a metal matrix composite material. Others are the same as in the first embodiment.
specific Embodiment approach 3
[0043] Embodiment 3: This embodiment is different from Embodiment 2 in that: the metal material is a superalloy. Others are the same as in the second embodiment.
[0044] The metal material described in this embodiment is not limited to superalloys, as long as the metal material has semi-solid structure characteristics, the present invention can be realized.
PUM
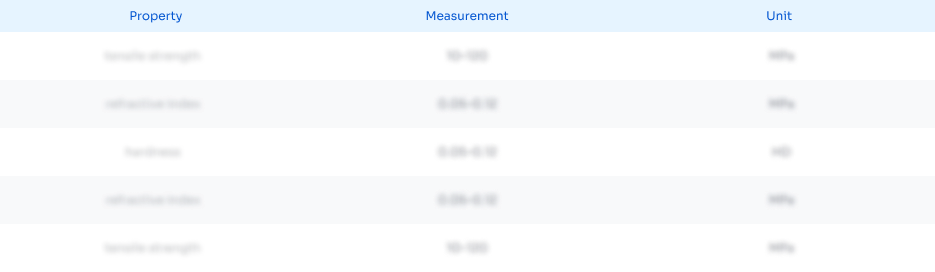
Abstract
Description
Claims
Application Information

- R&D
- Intellectual Property
- Life Sciences
- Materials
- Tech Scout
- Unparalleled Data Quality
- Higher Quality Content
- 60% Fewer Hallucinations
Browse by: Latest US Patents, China's latest patents, Technical Efficacy Thesaurus, Application Domain, Technology Topic, Popular Technical Reports.
© 2025 PatSnap. All rights reserved.Legal|Privacy policy|Modern Slavery Act Transparency Statement|Sitemap|About US| Contact US: help@patsnap.com