Centrifugal film coating apparatus
A coating film and equipment technology, applied in the field of microporous metal inner wall film preparation, can solve the problems of immature preparation methods of microporous inner wall film materials, and achieve the effect of simple structure, reasonable design, and easy operation
- Summary
- Abstract
- Description
- Claims
- Application Information
AI Technical Summary
Problems solved by technology
Method used
Image
Examples
Embodiment Construction
[0034] Such as figure 1 , figure 2 As shown, the present invention includes a base 1 and a centrifugal coating device installed on the base 1 . The centrifugal film coating device includes a film coating tool 2 which is arranged horizontally and continuously rotates while driving its internal materials to perform centrifugal movement, a transmission sleeve shaft 3 coaxially set on the outside of the film coating tool 2 and driving the film coating tool 2 to continuously rotate, The drive motor 4 connected to the drive sleeve shaft 3 through the transmission mechanism and the drive control system 5 connected to the drive motor 4 and controlling and adjusting the steering and rotation speed of the drive motor 4, the left and right ends of the drive sleeve shaft 3 Both are openings, and the transmission sleeve shaft 3 and the film coating tool 2 are assembled into one body by the detachable assembly part 1 and assembly part 2 respectively arranged between the left and right end...
PUM
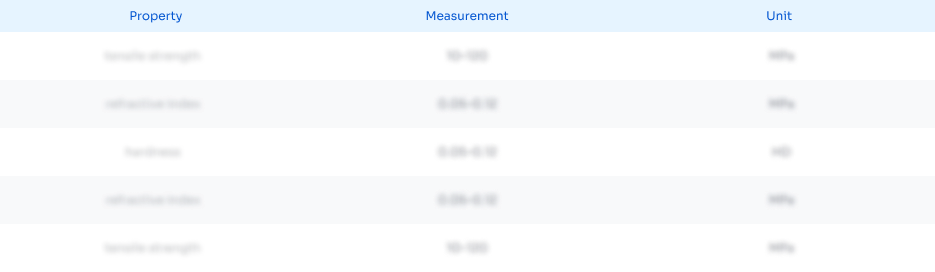
Abstract
Description
Claims
Application Information

- Generate Ideas
- Intellectual Property
- Life Sciences
- Materials
- Tech Scout
- Unparalleled Data Quality
- Higher Quality Content
- 60% Fewer Hallucinations
Browse by: Latest US Patents, China's latest patents, Technical Efficacy Thesaurus, Application Domain, Technology Topic, Popular Technical Reports.
© 2025 PatSnap. All rights reserved.Legal|Privacy policy|Modern Slavery Act Transparency Statement|Sitemap|About US| Contact US: help@patsnap.com