Ferrate/polyaniline magnetic nanometer catalytic agent and preparation method thereof
A magnetic nano and ferrite technology, applied in the field of material chemistry, can solve the problems of non-magnetism, non-selective adsorption performance of catalysts, and inability to easily recycle and recycle, and achieve excellent adsorption performance, excellent visible light catalytic activity, excellent Effect of Selective Adsorption Properties
- Summary
- Abstract
- Description
- Claims
- Application Information
AI Technical Summary
Problems solved by technology
Method used
Image
Examples
Embodiment 1
[0026] Example 1: Cobalt ferrite / polyaniline magnetic nano-catalyst, the preparation method that polyaniline content is 5wt%, comprises the following steps:
[0027] In the first step, ferric nitrate and cobalt nitrate with a mol ratio of 2:1 were stirred in ethanol for 90min;
[0028] In the second step, sodium hydroxide with a mol ratio of 80:1 to the cobalt nitrate added in step one is added to the solution obtained in the first step, and stirred for 60 min;
[0029] In the third step, react the mixed solution in the second step at 120°C for 12 hours, centrifuge and dry to obtain nano-cobalt ferrite;
[0030] The 4th step, the nano cobalt ferrite that ammonium persulfate and the 3rd step gained are dispersed in the hydrochloric acid solution that concentration is 0.5mol / L;
[0031] In the fifth step, add aniline with a molar ratio of 0.1 to the ammonium persulfate added in the fourth step to the system obtained in the fifth step, react at a temperature of 0°C for 24 h, a...
Embodiment 2
[0033] Example 2: Nickel ferrite / polyaniline magnetic nano-catalyst, the preparation method that polyaniline content is 90wt%, comprises the following steps:
[0034] The first step, be that ferric nitrate and nickel chloride of 2:1 are stirred 10min in ethanol with mol ratio;
[0035] In the second step, ammonia water having a molar ratio of 60:1 to the divalent transition metal salt added in step 1 is added to the solution obtained in the first step, and stirred for 10 min;
[0036] In the third step, the mixed solution in the second step was reacted at 140° C. for 24 h, then centrifuged and dried to obtain nano-nickel ferrite;
[0037] The 4th step, ammonium persulfate and the nano-nickel ferrite of the 3rd step gained are dispersed in the sulfuric acid solution that concentration is 1mol / L;
[0038] In the fifth step, aniline with a molar ratio of 10 to the ammonium persulfate added in the fourth step is added to the system obtained in the fifth step, and the reaction i...
Embodiment 3
[0039] Example 3: Copper ferrite / polyaniline magnetic nano-catalyst, the preparation method that polyaniline content is 10wt%, comprises the following steps:
[0040] In the first step, ferric nitrate and copper sulfate with a molar ratio of 2:1 were stirred in ethanol for 30 min;
[0041] In the second step, urea with a mol ratio of 40:1 to the divalent transition metal salt added in step one is added to the solution obtained in the first step, and stirred for 25 min;
[0042] In the third step, react the mixed solution in the second step at 160°C for 20 hours, then centrifuge and dry to obtain nano-copper ferrite;
[0043] The 4th step, the nano-copper ferrite that ammonium persulfate and the 3rd step gained are dispersed in the phosphoric acid solution that concentration is 2mol / L;
[0044] In the fifth step, aniline with a molar ratio of 1 to the ammonium persulfate added in the fourth step is added to the system obtained in the fifth step, and the reaction is carried out...
PUM
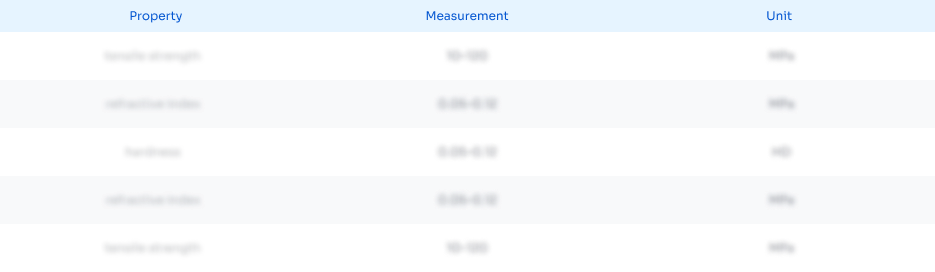
Abstract
Description
Claims
Application Information

- R&D Engineer
- R&D Manager
- IP Professional
- Industry Leading Data Capabilities
- Powerful AI technology
- Patent DNA Extraction
Browse by: Latest US Patents, China's latest patents, Technical Efficacy Thesaurus, Application Domain, Technology Topic, Popular Technical Reports.
© 2024 PatSnap. All rights reserved.Legal|Privacy policy|Modern Slavery Act Transparency Statement|Sitemap|About US| Contact US: help@patsnap.com