Manufacturing method for valve seat assembly
A manufacturing method and valve seat technology, applied in refrigeration components, lift valves, valve details, etc., can solve problems such as low processing efficiency, complex structure, looseness, etc., to ensure product quality, avoid interference and collision, and improve reliability.
- Summary
- Abstract
- Description
- Claims
- Application Information
AI Technical Summary
Problems solved by technology
Method used
Image
Examples
Embodiment Construction
[0044] The core of the present invention is to provide a manufacturing method of the valve seat assembly, which can not only position the valve seat and the cover more conveniently, but also ensure the coaxiality between the valve seat and the cover.
[0045] In order to enable those skilled in the art to better understand the technical solutions of the present invention, the present invention will be further described in detail below in conjunction with the accompanying drawings and specific embodiments.
[0046] Please refer to Figure 4 , Figure 4 It is a schematic structural diagram of an electronic expansion valve in an embodiment of the present invention.
[0047] Such as Figure 4As shown, the electronic expansion valve includes a valve seat 2, and the valve seat 2 is connected to the casing 53 through the cover 3; the casing 53 is provided with a magnet 54, and the magnet 54 is fixedly connected with the screw rod 55, and rotates along with the magnet 54 in a circum...
PUM
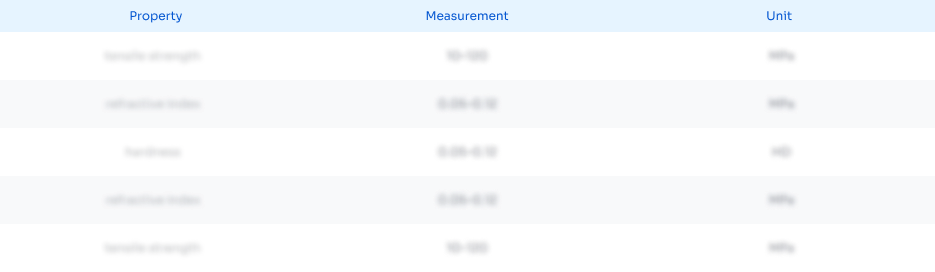
Abstract
Description
Claims
Application Information

- Generate Ideas
- Intellectual Property
- Life Sciences
- Materials
- Tech Scout
- Unparalleled Data Quality
- Higher Quality Content
- 60% Fewer Hallucinations
Browse by: Latest US Patents, China's latest patents, Technical Efficacy Thesaurus, Application Domain, Technology Topic, Popular Technical Reports.
© 2025 PatSnap. All rights reserved.Legal|Privacy policy|Modern Slavery Act Transparency Statement|Sitemap|About US| Contact US: help@patsnap.com