Catalyst for removing carbon monoxide, hydrocarbons and particulate matters in engine
A particulate matter and carbon monoxide technology, which is applied in metal/metal oxide/metal hydroxide catalysts, physical/chemical process catalysts, chemical/physical processes, etc., can solve the problems of preventing air pollution, ceramic filter performance degradation, Oxidation and other problems, to achieve excellent oxidation ability, excellent oxidation effect
- Summary
- Abstract
- Description
- Claims
- Application Information
AI Technical Summary
Problems solved by technology
Method used
Image
Examples
Embodiment 1
[0016] In order to prepare the Si-Ti-A-B composite catalyst, 50 g of ethylhexyloxyisopropoxide silicon as Si metal, 50 g of TiCl as Ti metal 4 , 5g of chloroplatinic acid as platinum group metal A, 5g of cesium nitrate as metal B of the 6th period, and 500g of 10% aqueous hydrochloric acid were mixed, and stirred for 3 hours at a temperature of 90°C at a speed of 60rpm to prepare Si- Ti-Pt-Cs composite catalyst; then, in the prepared Si-Ti-Pt-Cs composite catalyst, mix 10g of ethanol as alcohol and 10g of hexamethyldisilane as silane to prepare Si-Ti-Pt-Cs Composite catalyst coating solution; respectively make 2 porosity (porosity) be 30PPI and 3 porosity 50PPI, diameter is 7 inches, the foam body of Fe-Cr-Al material that thickness is 1 inch is impregnated in above-mentioned Si -Ti-Pt-Cs composite catalyst coating solution, dried at 110°C for 6 hours, then fired at 400°C for 2 hours to obtain Si-Ti-Pt-Cs composite for reducing soot at low temperature For the catalyst foam, t...
Embodiment 2
[0018]To prepare the Si-Ti-A-B composite catalyst, 50 g of silicon ethoxylate as Si metal, 50 g of tetraisopropoxytitanium as Ti metal, 5 g of ruthenium chloride as platinum group metal A, 5 g of ruthenium chloride as the 6th cycle The barium nitrate of metal B and the 10% sulfuric acid aqueous solution of 500g are mixed, stir 3 hours with the speed of 60rpm at the temperature of 90 ℃, thereby prepare Si-Ti-Ru-Ba composite catalyst; Then, to prepared Si-Ti -In the Ru-Ba composite catalyst, mix 10g of isopropanol as alcohol and 10g of phenylmethylsilane as silane to prepare Si-Ti-Ru-Ba composite catalyst coating solution; make 2 porosities of 30PPI and 3 respectively A stainless steel foam body with a porosity of 50PPI, a diameter of 7 inches, and a thickness of 1 inch is impregnated with the above-mentioned Si-Ti-Ru-Ba composite catalyst coating solution, dried at a temperature of 110° C. for 6 hours, and then dried at 400° C. ℃ for 2 hours to obtain the Si-Ti-Ru-Ba composite ...
Embodiment 3
[0020] To prepare the Si-Ti-A-B composite catalyst, 50 g of silicon ethoxylate as Si metal, 50 g of tetraisopropoxytitanium as Ti metal, 5 g of iridium chloride as platinum group metal A, 5 g as cycle 6 Ammonium tungstate of metal B and 500g of 10% nitric acid aqueous solution were mixed, stirred at a speed of 60rpm at a temperature of 90°C for 3 hours to prepare a Si-Ti-Ir-W composite catalyst; then, to the prepared Si- Mix 10g propanol as alcohol and 10g methyltrimethoxysilane as silane in the Ti-Ir-W composite catalyst to prepare Si-Ti-Ir-W composite catalyst coating solution; make 2 porosities of 30PPI and Three stainless steel foams with a porosity of 50PPI, a diameter of 7 inches, and a thickness of 1 inch were impregnated in the above-mentioned Si-Ti-Ir-W composite catalyst coating solution, dried at a temperature of 110°C for 6 hours, and then placed in a Fire at a temperature of 400°C for 2 hours to obtain a Si-Ti-Ir-W composite catalyst foam for reducing soot at low ...
PUM
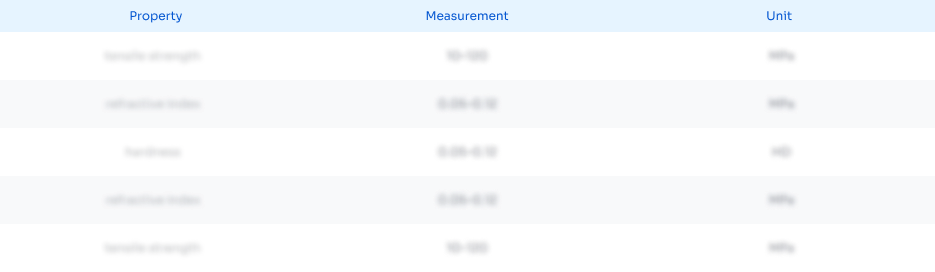
Abstract
Description
Claims
Application Information

- R&D Engineer
- R&D Manager
- IP Professional
- Industry Leading Data Capabilities
- Powerful AI technology
- Patent DNA Extraction
Browse by: Latest US Patents, China's latest patents, Technical Efficacy Thesaurus, Application Domain, Technology Topic, Popular Technical Reports.
© 2024 PatSnap. All rights reserved.Legal|Privacy policy|Modern Slavery Act Transparency Statement|Sitemap|About US| Contact US: help@patsnap.com