Imitation leather polishing treatment agent for synthetic leather and preparation method of imitation leather polishing treatment agent
A technology of imitating leather and treating agent, applied in leather surface treatment, small raw hide/large raw hide/leather/fur treatment, small raw hide/large raw hide/leather hide/fur chemical treatment, etc. The problems of high cost of spraying and complicated process can achieve the effect of simple production and preparation process, simple production equipment and simple construction process.
- Summary
- Abstract
- Description
- Claims
- Application Information
AI Technical Summary
Problems solved by technology
Method used
Examples
example 1
[0026] Example 1: 22% of 50-mode PU dry-process resin, 1% of quarter-second nitrocellulose, 9% of ultra-fine silicon dioxide, 1.2% of micronized polyethylene wax, 4% of oily organic fluorine water and oil repellent, castor 4% of sesame oil, 0.5% of silicone leveling and dispersing agent, and the balance of butanone. This example formula product is suitable for the imitation leather burnishing treatment of luggage leather.
[0027] The preparation method of the imitation leather burnishing treatment agent for synthetic leather of the present invention, the steps are: first add 1 / 4 second nitrocellulose to methyl ethyl ketone to make it dissolve completely in a disperser or a dispersing reactor, Add ultra-fine silica, micronized polyethylene wax and silicone dispersing and leveling agent to disperse at high speed for 10 minutes, then add castor oil, 50-mode PU dry-process resin, and organic fluorine waterproof and oil-repellent agent to disperse evenly.
example 2
[0028] Example 2: 20% of 50-mode PU dry-process resin, 2% of quarter-second nitrocellulose, 10% of ultra-fine silicon dioxide, 1.5% of micronized polyethylene wax, 4% of oily organic fluorine water and oil repellent, castor Sesame oil 5%, silicone leveling and dispersing agent 0.5%, balance butanone. The formula product of this example is suitable for the light-colored burnishing treatment of imitation leather of bag leather and shoe leather.
example 3
[0029] Example 3: 15% of 50-mode PU dry-process resin, 4% of quarter-second nitrocellulose, 8% of ultra-fine silicon dioxide, 1.8% of micronized polyethylene wax, 4% of oily organic fluorine water and oil repellent, castor Sesame oil 3%, silicone leveling and dispersing agent 0.5%, balance butanone. The formula product of this example is suitable for the high-gloss polishing treatment of imitation leather of bag leather and shoe leather.
PUM
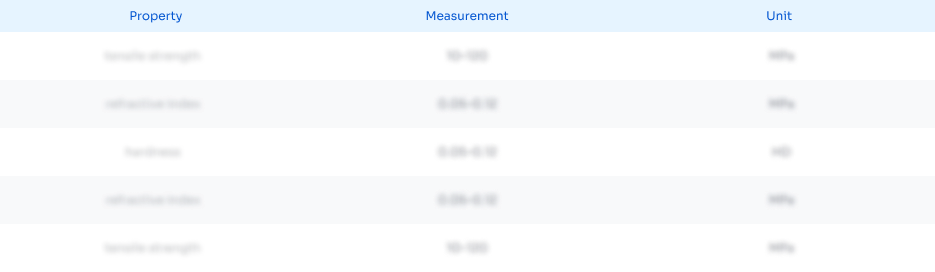
Abstract
Description
Claims
Application Information

- Generate Ideas
- Intellectual Property
- Life Sciences
- Materials
- Tech Scout
- Unparalleled Data Quality
- Higher Quality Content
- 60% Fewer Hallucinations
Browse by: Latest US Patents, China's latest patents, Technical Efficacy Thesaurus, Application Domain, Technology Topic, Popular Technical Reports.
© 2025 PatSnap. All rights reserved.Legal|Privacy policy|Modern Slavery Act Transparency Statement|Sitemap|About US| Contact US: help@patsnap.com