Scrimber comprising wood wool rod units and manufacturing method
A technology for recombining wood and wood wool, which is applied in the direction of household components, flat products, wood processing appliances, etc., can solve the problems of unsuccessful industrial production and popularization, difficulty in achieving ideal goals, and difficulty in compressive stress, and achieve easy mechanization and Automated production and control, the realization of mechanized and automated production and control, and the effect of improving the bonding strength
- Summary
- Abstract
- Description
- Claims
- Application Information
AI Technical Summary
Problems solved by technology
Method used
Image
Examples
Embodiment 1
[0028] Such as image 3 As shown, on a horizontally placed backing plate 4 with a format size of 700mm×1300mm, the method of directional paving and laying by step-type lamination or brick-wall lamination is adopted, and one or more layers of directional pavement are screened, After straightening, drying, and gluing, make a wood screw rod 2 of the same specification. The size specification of the wood screw rod is B×H×L=(0.5~3.0)mm×(0.5~3.0)mm×(50~500)mm ,Such as figure 2 . The so-called stepped laminated directional pavement refers to firstly orienting along the width direction of the slab, the length direction of the wood screw rods is parallel to the length direction of the slab, laying a row of wood screw rods neatly and evenly, and then moving half the wood screw rods to the length direction of the slab Rod length distance, and then lay a row of wood screw rods neatly and evenly along the width direction of the slab, and then repeat the above process until one or more l...
Embodiment 2
[0031] Such as figure 2 , image 3 , Figure 4 , Figure 5 , Figure 8As shown, on the backing plate 4 placed at the bottom of a molded box 8 of length × width × height = 1300mm × 700mm × 600mm, the wood screw rod 2 of the same specification will be made after screening, straightening, drying and gluing. The directional pavement and billet assembly method of stepped lamination or brick wall lamination is oriented and quantitatively positioned and paved layer by layer to a height of 600mm, and then sent to the upper platen 5 of the single-layer upper-press cold press equipped with a die 9 On the lower platen 6, after cold pressing (pressure F is 5×10 6 Pa, the cold pressing time is 30h; or the pressure F is 10×10 6 Pa, the cold pressing time is 15h; or the pressure F is 8×10 6 Pa, cold pressing time is 24h), pressure relief, and demoulding to make wood wool molded material 10, the length×width of wood wool molded material 10=1300mm×700mm, the height dimension is determin...
PUM
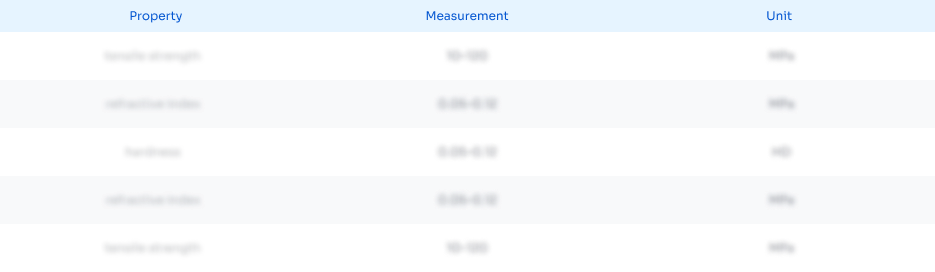
Abstract
Description
Claims
Application Information

- R&D Engineer
- R&D Manager
- IP Professional
- Industry Leading Data Capabilities
- Powerful AI technology
- Patent DNA Extraction
Browse by: Latest US Patents, China's latest patents, Technical Efficacy Thesaurus, Application Domain, Technology Topic, Popular Technical Reports.
© 2024 PatSnap. All rights reserved.Legal|Privacy policy|Modern Slavery Act Transparency Statement|Sitemap|About US| Contact US: help@patsnap.com