Method for coating micro/nano-metal powder by chemical vapor deposition
A technology of chemical vapor deposition and metal powder, applied in the direction of gaseous chemical plating, metal material coating process, coating, etc., can solve the problems of waste liquid generation, difficult industrial production, complicated operation process, etc., and reduce the ignition temperature , Improve the reaction rate and heat release, and the effect of high hydrophobicity
- Summary
- Abstract
- Description
- Claims
- Application Information
AI Technical Summary
Problems solved by technology
Method used
Image
Examples
Embodiment 1
[0039] 1), as attached figure 1 As shown, first, the cracking tube 4 is preheated, the temperature is raised to 300° C., and the temperature is kept constant for 25 minutes, and the temperature is realized by the temperature control system 10;
[0040]2), take 2g of aluminum powder with a particle size of 5 microns and add it to the reaction chamber 5, adjust the distance between the lower port of the cracking tube 4 and the aluminum powder to 1.5-2cm, use the vacuum pump 9 to evacuate the reaction chamber 5, and connect Cooling water 7 at 20°C is circulated for cooling;
[0041] 3), open the on-off valve of hexafluoropropylene oxide (HFPO) gas tank 1, regulate flow to 30sccm by pressure reducing valve 2 and flow meter 3, enter cracking tube 4, the difluorine that HFPO decomposes in cracking tube 4 produces Carbene (CF2) free radical.
[0042] 4) Difluorocarbene (CF2) free radicals produced by decomposition are polymerized on the surface of the aluminum powder to form a poly...
Embodiment 2
[0045] 1), first, preheat the cracking tube 4, the temperature reaches 350° C., and keeps the temperature constant for 25 minutes, and the temperature is realized by the temperature control system 10;
[0046] 2), take 2g of aluminum powder with a particle size of 1 micron and add it to the reaction chamber 5, adjust the distance between the 4 lower ports of the cracking tube and the aluminum powder between 1.5-2cm, and use the vacuum pump 9 to evacuate the reaction chamber 5 to make the reaction chamber 5 is in a vacuum state, and the cooling water 7 at 20°C is connected for circulating cooling;
[0047] Subsequent steps are the same as in Example 1.
Embodiment 3
[0049] 1), first, preheat the cracking tube 4, the temperature reaches 400°C, and keeps the temperature constant for 20 minutes, and the temperature is realized by the temperature control system 10;
[0050] 2), take 2g of boron powder with a particle size of 1 micron and add it to the reaction chamber 5, adjust the distance between the 4 openings of the cracking tube and the boron powder between 1.5-2cm, and use the vacuum pump 9 to evacuate the reaction chamber 5 to make the reaction chamber 5 In a vacuum state, turn on cooling water 7 at 20°C for circulating cooling, such as figure 1 shown.
[0051] Subsequent steps are the same as in Example 1.
PUM
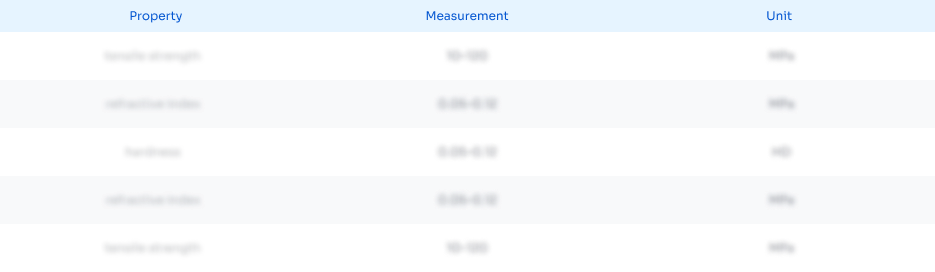
Abstract
Description
Claims
Application Information

- R&D
- Intellectual Property
- Life Sciences
- Materials
- Tech Scout
- Unparalleled Data Quality
- Higher Quality Content
- 60% Fewer Hallucinations
Browse by: Latest US Patents, China's latest patents, Technical Efficacy Thesaurus, Application Domain, Technology Topic, Popular Technical Reports.
© 2025 PatSnap. All rights reserved.Legal|Privacy policy|Modern Slavery Act Transparency Statement|Sitemap|About US| Contact US: help@patsnap.com