Passivation solution
A technology of passivation solution and sodium hydroxide, applied in the field of passivation solution, can solve the problems of hydrogen embrittlement of substrate and insufficient anti-corrosion performance of passivation solution, and achieve the effect of improving anti-corrosion performance and good anti-corrosion performance.
- Summary
- Abstract
- Description
- Claims
- Application Information
AI Technical Summary
Problems solved by technology
Method used
Examples
Embodiment 1
[0009] Embodiment 1: Take 1000g of pure water, add 17.75g of sodium hydroxide, 19.65g of sodium phosphate, 48g of phosphoric acid, and 96g of potassium dichromate. Stir it until completely dissolved and let it stand for half an hour. The passivation solution of this embodiment is used to passivate the martensitic stainless steel. Since the passivation treatment process is a common method for those skilled in the art, it will not be described in detail here. The passivated martensitic stainless steel of this embodiment is subjected to a salt spray test at a concentration of 5% sodium chloride and a temperature of 35° C. It can withstand 57 hours without corrosion, and its anti-corrosion performance is good. In addition, The passivation solution described in the present invention will not cause hydrogen embrittlement to martensitic stainless steel, will not cause adverse effects on other properties of martensitic stainless steel, so that the anti-corrosion performance of martens...
Embodiment 2
[0010] Embodiment two: sodium hydroxide 19.75g, sodium phosphate 21.65g, phosphoric acid 52g, potassium dichromate 104g. Stir it until completely dissolved and let it stand for half an hour. The passivation solution of this embodiment is used to passivate the martensitic stainless steel. Since the passivation treatment process is a common method for those skilled in the art, it will not be described in detail here. The passivated martensitic stainless steel of this embodiment is subjected to a salt spray test at a concentration of 5% sodium chloride and a temperature of 35°C. It can withstand 59 hours without corrosion, and its anti-corrosion performance is good. In addition, The passivation solution described in the present invention will not cause hydrogen embrittlement to martensitic stainless steel, will not cause adverse effects on other properties of martensitic stainless steel, so that the anti-corrosion performance of martensitic stainless steel is improved while its s...
Embodiment 3
[0011] Embodiment three: sodium hydroxide 18.25g, sodium phosphate 20.15g, phosphoric acid 49g, potassium dichromate 98g. Stir it until completely dissolved and let it stand for half an hour. The passivation solution of this embodiment is used to passivate the martensitic stainless steel. Since the passivation treatment process is a common method for those skilled in the art, it will not be described in detail here. The passivated martensitic stainless steel of this embodiment was subjected to a salt spray test at a concentration of 5% sodium chloride and a temperature of 35°C. It could withstand 58 hours without corrosion, and its corrosion resistance was good. In addition, this The passivation solution described in the invention will not cause hydrogen embrittlement to the martensitic stainless steel, and will not cause adverse effects on other properties of the martensitic stainless steel, so that the anti-corrosion performance of the martensitic stainless steel is improved...
PUM
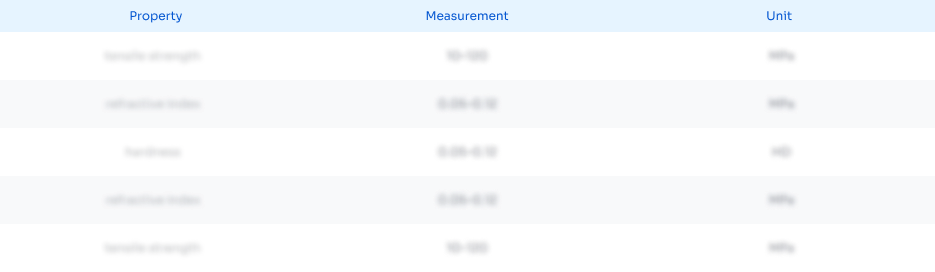
Abstract
Description
Claims
Application Information

- R&D Engineer
- R&D Manager
- IP Professional
- Industry Leading Data Capabilities
- Powerful AI technology
- Patent DNA Extraction
Browse by: Latest US Patents, China's latest patents, Technical Efficacy Thesaurus, Application Domain, Technology Topic, Popular Technical Reports.
© 2024 PatSnap. All rights reserved.Legal|Privacy policy|Modern Slavery Act Transparency Statement|Sitemap|About US| Contact US: help@patsnap.com