Nano high-air-tightness compressive film and preparation method thereof
A high-air-tight, pressure-resistant film technology, applied in the field of pressure-resistant films, can solve the problems of air-tightness and pressure-resistant performance limitations, inability to use pressure-resistant equipment, inconvenient to carry, etc., to improve air-tightness and excellent physical properties. Mechanical properties, the effect of good compressive strength
- Summary
- Abstract
- Description
- Claims
- Application Information
AI Technical Summary
Problems solved by technology
Method used
Examples
preparation example Construction
[0042] The preparation method of the nano high airtight anti-pressure film described in the present invention comprises the following steps:
[0043] Step 1. Calendering process: Add PVC polyvinyl chloride resin and modified nano-kaolin to a high-speed mixer and stir evenly, then add DOP dioctyl phthalate, DBP dibutyl phthalate, DCHP dibutyl phthalate Cyclohexyl ester, stabilizer, calcium carbonate and other additives are evenly mixed and then added to a calendering machine for calendering to obtain an embryonic film;
[0044] Step 2. Bonding process: use the pretreated polyester mesh as the middle layer, and set up a layer of embryo film prepared in step 1 on the upper and lower layers. Send the three-layer film from the film sending rack to the laminating machine. After fully preheating at 140-150°C, the three layers of membranes are pasted together in the order of the upper embryonic membrane, polyester mesh and lower embryonic membrane. The upper embryonic membrane is in c...
Embodiment 1
[0047] Components and weights thereof of the nano high airtight anti-pressure film are:
[0048] PVC polyvinyl chloride resin 100 kg;
[0049] DOP dioctyl phthalate 10 kg;
[0050] DBP dibutyl phthalate 10 kg;
[0051] DCHP dicyclohexyl phthalate 10 kg;
[0052] Barium, zinc composite stabilizer 3 kg;
[0053] Modified nano kaolin 5 kg;
[0054] Calcium carbonate 5 kg;
[0055] Pigment 1 kg.
[0056] The preparation method of the nano high airtight anti-pressure film described in the present invention comprises the following steps:
[0057] Step 1. Calendering process: Add PVC polyvinyl chloride resin and modified nano-kaolin to a high-speed mixer and stir evenly, then add DOP dioctyl phthalate, DBP dibutyl phthalate, DCHP dibutyl phthalate Cyclohexyl ester, stabilizer, calcium carbonate and other additives were mixed evenly and added to a calender molding machine for calendering to obtain an embryo film; the calendering temperature was 170°C, and the pulling speed was ...
Embodiment 2
[0066] Components and weights thereof of the nano high airtight anti-pressure film are:
[0067] PVC polyvinyl chloride resin 100 kg;
[0068] DOP dioctyl phthalate 25 kg;
[0069] DBP dibutyl phthalate 25 kg;
[0070] DCHP dicyclohexyl phthalate 15 kg;
[0071] Tin methyl mercaptide heat stabilizer 5 kg;
[0072] Modified nano kaolin 15 kg;
[0073] Calcium carbonate 15 kg;
[0074] Other additives 3 kg.
[0075] The preparation method of the nano high airtight anti-pressure film described in the present invention comprises the following steps:
[0076] Step 1. Calendering process: Add PVC polyvinyl chloride resin and modified nano-kaolin to a high-speed mixer and stir evenly, then add DOP dioctyl phthalate, DBP dibutyl phthalate, DCHP dibutyl phthalate Cyclohexyl ester, stabilizer, calcium carbonate and other additives were mixed evenly and added to a calender molding machine for calendering to obtain an embryo film; the calendering temperature was 180°C, and the pull...
PUM
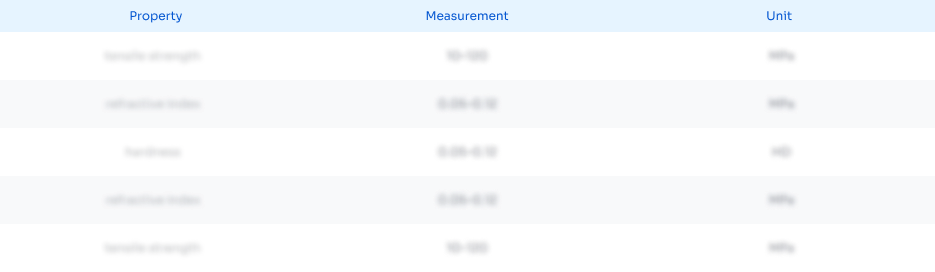
Abstract
Description
Claims
Application Information

- R&D
- Intellectual Property
- Life Sciences
- Materials
- Tech Scout
- Unparalleled Data Quality
- Higher Quality Content
- 60% Fewer Hallucinations
Browse by: Latest US Patents, China's latest patents, Technical Efficacy Thesaurus, Application Domain, Technology Topic, Popular Technical Reports.
© 2025 PatSnap. All rights reserved.Legal|Privacy policy|Modern Slavery Act Transparency Statement|Sitemap|About US| Contact US: help@patsnap.com