Liquid metal knife cutting system
A liquid metal, cutting system technology, applied in metal processing equipment, abrasives, abrasive jet machine tools, etc., can solve problems such as high noise and easy wear, and achieve the effect of reducing industrial water use
- Summary
- Abstract
- Description
- Claims
- Application Information
AI Technical Summary
Problems solved by technology
Method used
Image
Examples
Embodiment 1
[0042] image 3 It is the structural representation of the liquid metal knife cutting system (embodiment 1) of the present invention; Fig. 1 (b) is the structural representation of cutting device 3; As can be seen from the figure, the liquid metal knife cutting system of the present embodiment comprises: a built-in A liquid metal storage tank 1 for liquid metal, a booster pump 2, a cutting device 3, a workbench 5, a liquid metal recovery container 6 and a numerical control table 9;
[0043] Such as figure 2 As shown, the cutting device 3 includes:
[0044] A cutting nozzle 31 with a diameter of 0.01-10 mm and a rectifying cavity 33 connected to the upper end of the cutting nozzle 31; the rectifying cavity 33 is a trapezoidal cavity with a large upper volume and a small lower volume; There is a liquid metal inlet pipe 34 communicating with the outlet of the booster pump 2 through a flexible silicone tube 11; an observation hole is also opened on the side wall of the rectifyin...
Embodiment 2
[0052] Fig. 1 (a) is the structural representation of the liquid metal knife cutting system of the present embodiment; Fig. 1 (b) is the structural representation of cutting device 3; As can be seen from the figure, the liquid metal knife cutting system of the present embodiment is different from Embodiment 1 What is more: also includes the abrasive material inlet pipe 35 that is installed on the upper part of the rectifying chamber 33, the abrasive material inlet pipe 35 communicates with the abrasive material feeder 12 with the abrasive material control valve 13; the liquid metal recovery container 6 is connected with the recovery pump 7 is equipped with a liquid-solid separation device 14 communicating with the abrasive feeder 12 on the connecting pipeline connected with each other.
Embodiment 3
[0054] image 3 It is the structural representation of the liquid metal knife cutting system of the present embodiment; Fig. 1 (b) is the structural representation of the cutting device 3; As can be seen from the figure, the liquid metal knife cutting system of the present embodiment is different from Embodiment 2 in that it also includes The vacuum cover 15 installed on the workbench 5 covers the workpiece 4 to be cut and the cutting nozzle 31 placed on the workbench 5 .
PUM
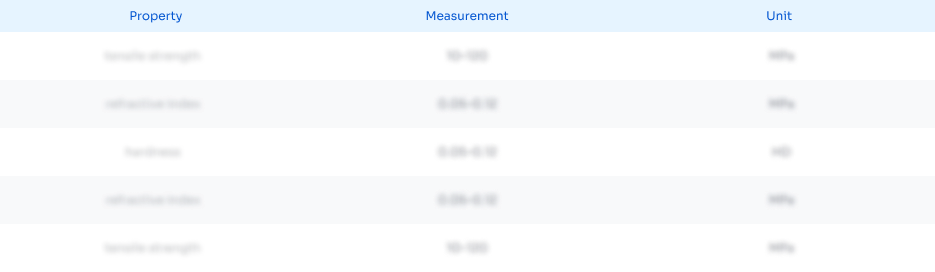
Abstract
Description
Claims
Application Information

- R&D
- Intellectual Property
- Life Sciences
- Materials
- Tech Scout
- Unparalleled Data Quality
- Higher Quality Content
- 60% Fewer Hallucinations
Browse by: Latest US Patents, China's latest patents, Technical Efficacy Thesaurus, Application Domain, Technology Topic, Popular Technical Reports.
© 2025 PatSnap. All rights reserved.Legal|Privacy policy|Modern Slavery Act Transparency Statement|Sitemap|About US| Contact US: help@patsnap.com