Milling finish machining method based on dynamic rigidity of impeller blade
A technology of impeller blades and dynamic stiffness, which is applied in the field of mechanical processing, can solve the problems that do not involve the importance of suppression, achieve the effect of improving processing stability and solving cutting chatter
- Summary
- Abstract
- Description
- Claims
- Application Information
AI Technical Summary
Problems solved by technology
Method used
Image
Examples
Embodiment Construction
[0017] The content of the milling finishing method based on the dynamic stiffness of the impeller blade according to the present invention is to obtain the dynamic mode (damping ratio, stiffness, natural frequency, effective mass) of the impeller blade through the standard modal test, and then introduce flutter The model can be used to obtain the stability criterion, so as to obtain reasonable processing parameters.
[0018] The present invention will be further described below in conjunction with the accompanying drawings, and the details of each step will be set forth.
[0019] Processing method of the present invention comprises the steps:
[0020] Step 1: Modal test to determine the dynamic mode of the impeller blade: the principle is as follows figure 1 As shown in , the standard hammer impact test is adopted, by collecting the impact excitation signal of the hammer and the response signal of the acceleration sensor, aiming at the changing wall thickness t 1 , t 2 and ...
PUM
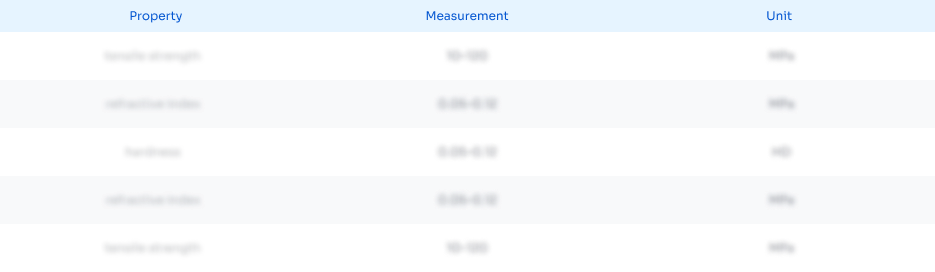
Abstract
Description
Claims
Application Information

- Generate Ideas
- Intellectual Property
- Life Sciences
- Materials
- Tech Scout
- Unparalleled Data Quality
- Higher Quality Content
- 60% Fewer Hallucinations
Browse by: Latest US Patents, China's latest patents, Technical Efficacy Thesaurus, Application Domain, Technology Topic, Popular Technical Reports.
© 2025 PatSnap. All rights reserved.Legal|Privacy policy|Modern Slavery Act Transparency Statement|Sitemap|About US| Contact US: help@patsnap.com