Device and method for installing and adjusting reference grating of lithography equipment
A technology for reference gratings and lithography equipment, applied in the field of integrated circuit manufacturing equipment manufacturing, can solve problems such as increasing alignment errors, and achieve the effect of reducing assembly and adjustment errors
- Summary
- Abstract
- Description
- Claims
- Application Information
AI Technical Summary
Problems solved by technology
Method used
Image
Examples
Embodiment Construction
[0047] Specific embodiments of the present invention will be described in detail below in conjunction with the accompanying drawings.
[0048] In order to overcome the technical problem in the prior art that the focal plane position found in the actual focusing process and the actual focal plane position have a deviation, a light intensity correction device is added to the grating assembly and adjustment device. The light intensity calibration device is used to adjust the output light intensity of the laser light source, to ensure that the light intensity transmitted through the vibrating mirror remains constant, and to reduce the adjustment error of the reference grating caused by the change of the projected light intensity caused by the vibrating mirror swing.
[0049] as attached figure 2 shown in the attached figure 2 It is a structural schematic diagram of the light intensity correction device disclosed in the present invention. The light intensity calibration device in...
PUM
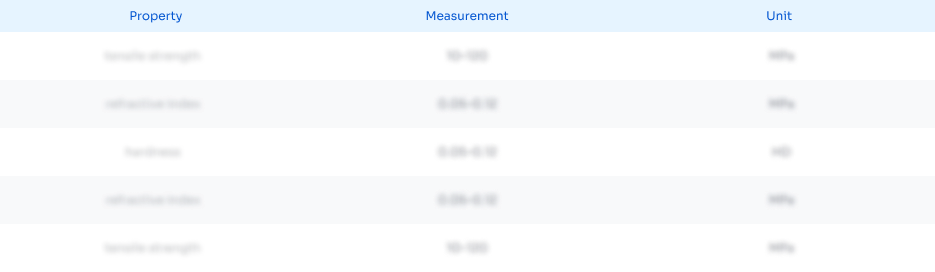
Abstract
Description
Claims
Application Information

- R&D
- Intellectual Property
- Life Sciences
- Materials
- Tech Scout
- Unparalleled Data Quality
- Higher Quality Content
- 60% Fewer Hallucinations
Browse by: Latest US Patents, China's latest patents, Technical Efficacy Thesaurus, Application Domain, Technology Topic, Popular Technical Reports.
© 2025 PatSnap. All rights reserved.Legal|Privacy policy|Modern Slavery Act Transparency Statement|Sitemap|About US| Contact US: help@patsnap.com