Method for treating pyrite cinder by combining acidic leaching with alkaline dissolving
A technology for pyrite slag and combined treatment, which is applied in the field of acid leaching-alkali-dissolving combined treatment of pyrite slag and red mud, and can solve the problems of large investment, low iron utilization rate, secondary pollution, etc.
- Summary
- Abstract
- Description
- Claims
- Application Information
AI Technical Summary
Problems solved by technology
Method used
Image
Examples
Embodiment Construction
[0026] The specific embodiment of the present invention will be described in detail below in conjunction with the process flow chart.
[0027] Pyrite slag is the waste residue produced in the production process of sulfuric acid from pyrite, which is rich in iron resources, and the general grade is between 40% and 64%. When the silicon dioxide content in the pyrite slag is less than 10%, the total iron content in the nitric acid leaching slag can reach about 60%, and no further treatment can meet the requirements of iron concentrate; when the silicon dioxide content is 10% When the content of silicon dioxide is greater than 15%, the total iron content in nitric acid leaching slag can reach about 55%, which can meet the requirements of general iron concentrate; when the silica content is greater than 15%, the total iron content in nitric acid leaching slag can reach 50 %, it needs to be further processed by alkali dissolution.
[0028] With reference to process flow chart, the ...
PUM
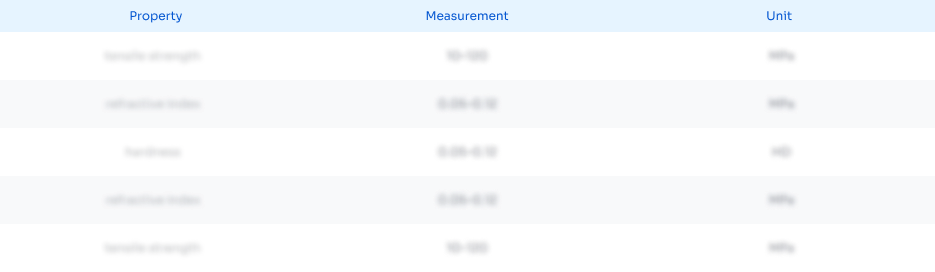
Abstract
Description
Claims
Application Information

- R&D
- Intellectual Property
- Life Sciences
- Materials
- Tech Scout
- Unparalleled Data Quality
- Higher Quality Content
- 60% Fewer Hallucinations
Browse by: Latest US Patents, China's latest patents, Technical Efficacy Thesaurus, Application Domain, Technology Topic, Popular Technical Reports.
© 2025 PatSnap. All rights reserved.Legal|Privacy policy|Modern Slavery Act Transparency Statement|Sitemap|About US| Contact US: help@patsnap.com