Method for preparing titanyl sulfate solution with flotation ilmenite
A technology of titanium oxysulfate and titanium concentrate, applied in the direction of titanium oxide/hydroxide, titanium dioxide, etc., can solve problems such as affecting the operation safety of employees, hidden dangers of employee operation safety, and asynchronous reaction, so as to reduce labor operation intensity and improve Environmental sanitation, the effect of avoiding waste of resources
- Summary
- Abstract
- Description
- Claims
- Application Information
AI Technical Summary
Problems solved by technology
Method used
Examples
specific Embodiment approach
[0022] The specific embodiment of the present invention is as follows: a kind of method that prepares titanyl sulfate solution with flotation titanium concentrate, comprises the steps:
[0023] a. Mix titanium concentrate ore powder and concentrated sulfuric acid evenly;
[0024] b. Put the evenly mixed ilmenite ore powder and concentrated sulfuric acid in the acid hydrolysis pot, add the initiator solution to initiate the mineral acid reaction; when the mineral acid reacts until a large number of bubbles are formed in the acid hydrolysis pot, add a defoamer to the acid hydrolysis pot;
[0025] c. After the mixture after the mineral acid reaction is matured, add a leaching solution into the acid hydrolysis pot for leaching, and then filter to obtain a titanyl sulfate solution.
[0026] Those skilled in the art can understand that the acidolysis pot is an environment of high temperature and strong acid, and the defoamer added should of course be a defoamer resistant to high tem...
Embodiment 1
[0037] The flotation titanium concentrate is ground by air-sweeping mill, and the fineness of the ore powder reaches 325 mesh sieve, and the remaining 25% is sent to the post-grinding bin for cooling, and the temperature is lowered to 50°C, and then sent to the ore powder metering tank. When feeding, measure 30 tons of ore powder. The content of titanium dioxide in the ore powder is 46.2%. The temperature in the mixing tank is about 42°C, and it is sent to 140m after pre-mixing 3 In the acidolysis pot, the heat generated by diluting the mineral acid mixture with 4.21 tons of water initiates the mineral acid reaction. When the temperature rose to 175°C, a large number of bubbles began to be generated in the acid hydrolysis pot, and 60kg of D313 defoamer was added to the acid hydrolysis pot. The D313 defoamer came from Dow Corning Co., Ltd. During the reaction, no material was sprayed out of the acidolysis pot. After aging for 90 minutes, the temperature of the material droppe...
Embodiment 2
[0039] The flotation titanium concentrate is ground by wind sweeping mill, and the fineness of the ore powder reaches 325 mesh sieve, and the remaining 5% is sent to the post-grinding bin for cooling, and the temperature is lowered to 50°C, and then sent to the ore powder metering tank. When feeding, measure 30 tons of ore powder, the content of titanium dioxide in the ore powder is 46.2%, pre-mix the ore powder and 50.82 tons of 91.5% concentrated sulfuric acid in the pre-mixing tank for 10 minutes, and the temperature of the added concentrated sulfuric acid is 40°C. The temperature in the mixing tank is about 42°C, and it is sent to 140m after pre-mixing 3 In the acidolysis pot, the heat generated by diluting the mineral acid mixture with 4.21 tons of water initiates the mineral acid reaction. When the temperature rose to 175°C, a large number of bubbles began to be generated in the acid hydrolysis pot, and 75kg of D313 defoamer was added. The D313 defoamer came from Dow Cor...
PUM
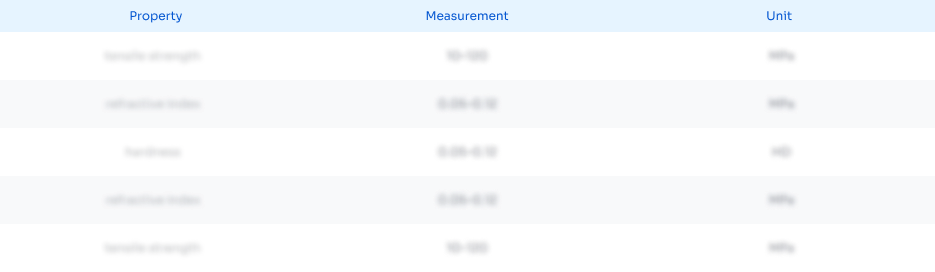
Abstract
Description
Claims
Application Information

- R&D Engineer
- R&D Manager
- IP Professional
- Industry Leading Data Capabilities
- Powerful AI technology
- Patent DNA Extraction
Browse by: Latest US Patents, China's latest patents, Technical Efficacy Thesaurus, Application Domain, Technology Topic, Popular Technical Reports.
© 2024 PatSnap. All rights reserved.Legal|Privacy policy|Modern Slavery Act Transparency Statement|Sitemap|About US| Contact US: help@patsnap.com