Rolling oil for stainless steel
A rolling oil, stainless steel technology, applied in the petroleum industry, lubricating compositions, etc., can solve the problems of high price of sulfur and phosphorus additives, unattainable process quality, only one-time use, etc., to achieve good anti-oxidation effect and good lubrication Sexuality, toxicity-reducing effect
- Summary
- Abstract
- Description
- Claims
- Application Information
AI Technical Summary
Problems solved by technology
Method used
Image
Examples
Embodiment Construction
[0011] A kind of preparation of stainless steel rolling oil, which is composed of the following raw materials by weight: 76.2% white oil, 12% neopentyl glycol ester, 6% pentaerythritol fatty acid ester, 2% isooctyl stearate , 0.8% mixed high temperature antioxidant, 0.2% 2.6 di-tert-butyl-p-cresol, 0.1% dipotassium EDTA, 0.5% T711, 0.2% T551, 2% T306.
[0012] Among them: the mixed high-temperature antioxidant is compounded by diisooctyldiphenylamine and mono-tert-octyl-α-naphthylamine, and the ratio of the two is diisooctyldiphenylamine:mono-tert-octylphenyl-α - Naphthylamine = 1.7:1.0. The white oil adopts 7#-10# white oil; the viscosity of the neopentyl polyol ester is 40°C (6.0~22mm 2 / s).
[0013] The blending process is as follows: firstly, the white oil of the formula quantity is put into a stainless steel (non-magnetic) blending kettle, and then the temperature is gradually raised to 80°C. During the heating process, the mixed antioxidant, 2.6 di-tert-butyl-p-cresol...
PUM
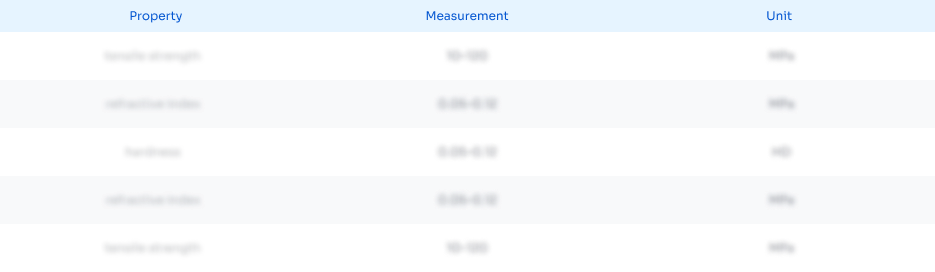
Abstract
Description
Claims
Application Information

- R&D
- Intellectual Property
- Life Sciences
- Materials
- Tech Scout
- Unparalleled Data Quality
- Higher Quality Content
- 60% Fewer Hallucinations
Browse by: Latest US Patents, China's latest patents, Technical Efficacy Thesaurus, Application Domain, Technology Topic, Popular Technical Reports.
© 2025 PatSnap. All rights reserved.Legal|Privacy policy|Modern Slavery Act Transparency Statement|Sitemap|About US| Contact US: help@patsnap.com