Manufacturing process for printed circuit board
A printed circuit board and manufacturing process technology, applied in the direction of printed circuit manufacturing, printed circuits, and assembling printed circuits with electrical components
- Summary
- Abstract
- Description
- Claims
- Application Information
AI Technical Summary
Problems solved by technology
Method used
Examples
specific Embodiment approach 1
[0011] Specific implementation mode one, Step 1. Preparation of base material and negative film: (1) Before production, the light-painted negative film should be carefully inspected. For the 9"X 11" size film, use the OPTI LINE film punching machine to punch the inner film. The outer negative is to be reproduced as a diazo film. The 11"X 14" size board film adopts the L-shaped positioning method, and uses the C·A·PICARD punching equipment to punch the positioning holes. (2) Stick film. Attach the anti-corrosion dry film to the clean copper foil surface by hot pressing with a film sticking machine. (3) Substrate punching. After the substrate with the dry film has cooled, punch the 9"X 11" board with the ACCU.LINE substrate punch. The L-shaped positioning method omits this step. (4) Exposure. Adhere the negative on the film surface and expose it to transfer the pattern to the copper surface. (5) Development. The unexposed and cured dry film is removed by chemical method...
specific Embodiment approach 2
[0015] Specific implementation mode two, Step 1. Preparation of base material and negative film: (1) Before production, the light-painted negative film should be carefully inspected. For the 9"X 11" size film, use the OPTI LINE film punching machine to punch the inner film. The outer negative is to be reproduced as a diazo film. The 11"X 14" size board film uses the L-shaped positioning method, and uses the C·A·PICARD punching equipment to punch the positioning holes. (2) Stick film. Attach the anti-corrosion dry film to the clean copper foil surface by hot pressing with a film sticking machine. (3) Substrate punching. After the substrate with the dry film has cooled, punch the 9"X 11" board with the ACCU.LINE substrate punch. The L-shaped positioning method omits this step. (4) Exposure. Adhere the negative on the film surface and expose it to transfer the pattern to the copper surface. (5) Development. The unexposed and cured dry film is removed by chemical methods...
specific Embodiment approach 3
[0019] Specific implementation mode three, Step 1. Preparation of base material and negative film: (1) Before production, the light-painted negative film should be carefully inspected. For the 9"X 11" size film, use the OPTI LINE film punching machine to punch the inner film. The outer negative is to be reproduced as a diazo film. The 11"X 14" size board film uses the L-shaped positioning method, and uses the C·A·PICARD punching equipment to punch the positioning holes. (2) Stick film. Attach the anti-corrosion dry film to the clean copper foil surface by hot pressing with a film sticking machine. (3) Substrate punching. After the substrate with the dry film has cooled, punch the 9"X 11" board with the ACCU.LINE substrate punch. The L-shaped positioning method omits this step. (4) Exposure. Adhere the negative on the film surface and expose it to transfer the pattern to the copper surface. (5) Development. The unexposed and cured dry film is removed by chemical metho...
PUM
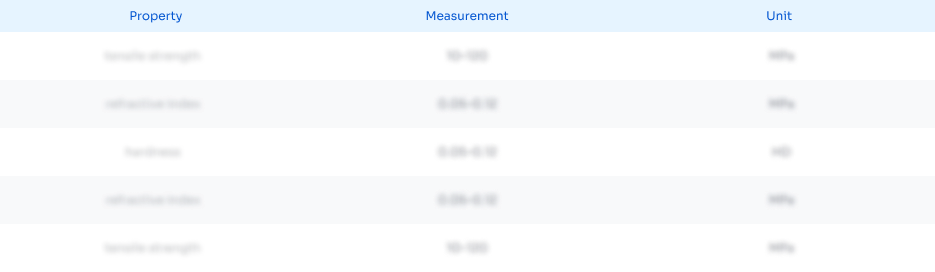
Abstract
Description
Claims
Application Information

- R&D
- Intellectual Property
- Life Sciences
- Materials
- Tech Scout
- Unparalleled Data Quality
- Higher Quality Content
- 60% Fewer Hallucinations
Browse by: Latest US Patents, China's latest patents, Technical Efficacy Thesaurus, Application Domain, Technology Topic, Popular Technical Reports.
© 2025 PatSnap. All rights reserved.Legal|Privacy policy|Modern Slavery Act Transparency Statement|Sitemap|About US| Contact US: help@patsnap.com