Cutting method for copper clad aluminum busbar
A copper-clad aluminum bar and cutting equipment technology, applied in the field of copper-clad aluminum bar cutting, can solve the problems of large cutting volume, affecting product accuracy, affecting appearance and oxidation resistance, etc., and achieves the effect of high plasticity
- Summary
- Abstract
- Description
- Claims
- Application Information
AI Technical Summary
Problems solved by technology
Method used
Image
Examples
Embodiment Construction
[0019] The copper-clad aluminum bar cutting method of the present invention first utilizes the oblong ends of the upper and lower mold cores of the copper-clad aluminum bar cutting equipment to symmetrically punch out round dimple-shaped grooves on both sides of the middle part of the copper-clad aluminum bar, relying on the high plasticity of the copper cladding material , the tensile strength, elongation, yield strength, shear strength, Brinell hardness and other strength characteristics are better than the inner aluminum core material. The aluminum core squeezes both sides of the circular ends of the upper and lower mold cores; at this time, the circular ends of the upper and lower mold cores simultaneously stamp the copper outer cladding with the same pressure from the opposite direction. Excellent plasticity, stretching and deforming into a circular dimple-shaped groove, and at the same time, it transmits and disperses the stamping force to the inner aluminum core. The ten...
PUM
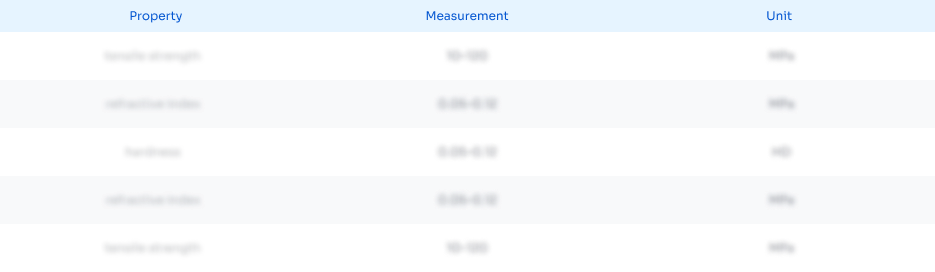
Abstract
Description
Claims
Application Information

- R&D
- Intellectual Property
- Life Sciences
- Materials
- Tech Scout
- Unparalleled Data Quality
- Higher Quality Content
- 60% Fewer Hallucinations
Browse by: Latest US Patents, China's latest patents, Technical Efficacy Thesaurus, Application Domain, Technology Topic, Popular Technical Reports.
© 2025 PatSnap. All rights reserved.Legal|Privacy policy|Modern Slavery Act Transparency Statement|Sitemap|About US| Contact US: help@patsnap.com