Steel tube as well as processing method and processing equipment for steel tube
A processing method and technology of processing equipment, which are applied in the field of steel pipes, can solve the problems of not being able to achieve the wear resistance of steel pipes and ensuring toughness, safety hazards, and bursting of the hardening point of pipe fittings.
- Summary
- Abstract
- Description
- Claims
- Application Information
AI Technical Summary
Problems solved by technology
Method used
Image
Examples
Embodiment Construction
[0030] Specific embodiments of the present invention will be described in detail below in conjunction with the accompanying drawings. It should be understood that the specific embodiments described here are only used to illustrate and explain the present invention, and are not intended to limit the present invention.
[0031] According to the present invention, a method for processing a steel pipe is provided. The method for processing a steel pipe includes: an inner wall quenching process, the inner wall quenching process includes quenching the inner wall of the steel pipe, so that the steel pipe as a whole forms a martensitic structure; and an outer wall tempering process, the outer wall The tempering process includes tempering the outer wall of the steel pipe processed by the inner wall quenching process at a medium temperature, so that the outer wall of the steel pipe forms a tempered troostite structure, and the outer wall tempering process of the present invention also in...
PUM
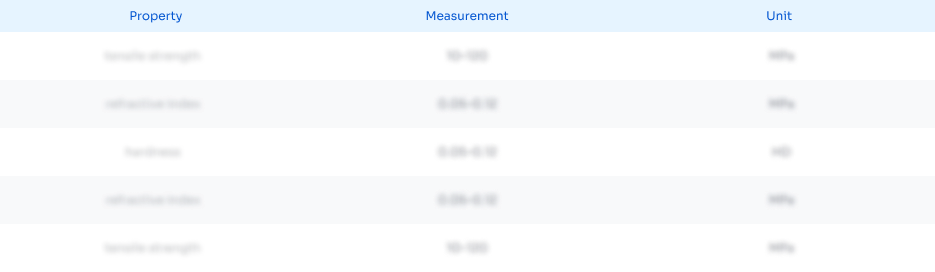
Abstract
Description
Claims
Application Information

- Generate Ideas
- Intellectual Property
- Life Sciences
- Materials
- Tech Scout
- Unparalleled Data Quality
- Higher Quality Content
- 60% Fewer Hallucinations
Browse by: Latest US Patents, China's latest patents, Technical Efficacy Thesaurus, Application Domain, Technology Topic, Popular Technical Reports.
© 2025 PatSnap. All rights reserved.Legal|Privacy policy|Modern Slavery Act Transparency Statement|Sitemap|About US| Contact US: help@patsnap.com