Method for preparing medium aluminum grinding balls by secondary ball milling
A technology of secondary ball milling and grinding balls, applied in chemical instruments and methods, other chemical processes, etc., can solve the problems of low ball milling efficiency, long ball milling time, high labor intensity, etc., to improve the output of grinding balls and chemical stability Good, the effect of improving product quality
- Summary
- Abstract
- Description
- Claims
- Application Information
AI Technical Summary
Problems solved by technology
Method used
Examples
Embodiment 1
[0023] Embodiment 1: a kind of method for secondary ball milling to prepare medium aluminum grinding balls, comprising the following steps:
[0024] (1) Grinding: Weigh 88% of cooked bauxite, 4% of dolomite, 4% of porcelain stone, 3% of clay, and 1% of sodium humate; the cooked bauxite includes aluminum content of 72-73%, 74% -75%, 77-78% three kinds of cooked bauxite, the weight ratios are 34%, 21% and 33% respectively;
[0025] Crush the blocky raw materials to less than 3mm, put them into the ball mill, then add water according to the weight ratio of raw materials and water 7:3, add 3-5‰ dispersant sodium tripolyphosphate and 3-5‰ poly Vinyl alcohol solution, start ball milling, the speed of the ball mill is 16-20r / min, the slurry is sieved with a 500-mesh standard sample sieve, the sieve residue is below 0.2%, and stale after 8-12h; the mass concentration of the polyvinyl alcohol solution 5%;
[0026] The ball milling adopts the second ball milling method. Two kinds of g...
Embodiment 2
[0031] Embodiment 2: basically the same as Embodiment 1, the difference is:
[0032] (1) Grinding: raw materials cooked bauxite 88%, dolomite 3%, porcelain stone 4%, clay 3%, sodium humate 2%, of which the cooked bauxite includes aluminum content of 72%, 74%, 77% Three kinds of cooked bauxite, the weight ratios are 34%, 21% and 33% respectively; plus 4‰ dispersant sodium tripolyphosphate and 4‰ polyvinyl alcohol solution;
[0033] (2) Molding: Molding pressure is 400MPa, hold pressure for 3-5 seconds.
[0034] All the other steps are the same as Example 1 such as steps such as secondary ball milling method, granulation, and firing.
Embodiment 3
[0035] Embodiment 3: Aluminum grinding ball and preparation method thereof are basically the same as Example 1, except that:
[0036] (1) Grinding: 88% cooked bauxite, 5% dolomite, 2% porcelain stone, 4% clay, 1% sodium humate, among which cooked bauxite includes aluminum content of 73%, 75%, 77% Three kinds of cooked bauxite, the weight ratios are 34%, 21% and 33% respectively; plus 5‰ dispersant sodium tripolyphosphate and 3‰ polyvinyl alcohol solution;
[0037] (2) Molding: Molding pressure is 390MPa, hold pressure for 3-5 seconds.
[0038] All the other steps are the same as Example 1 such as steps such as secondary ball milling method, granulation, and firing.
PUM
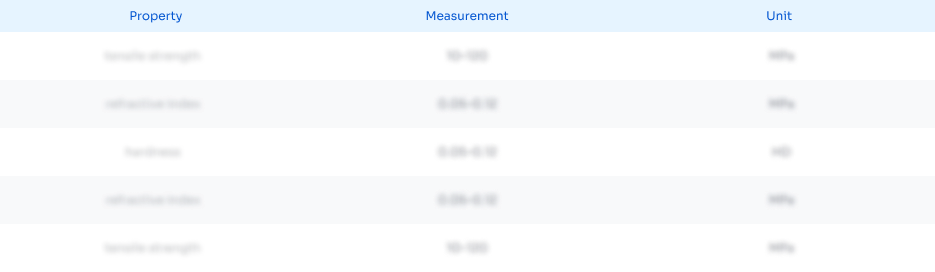
Abstract
Description
Claims
Application Information

- R&D
- Intellectual Property
- Life Sciences
- Materials
- Tech Scout
- Unparalleled Data Quality
- Higher Quality Content
- 60% Fewer Hallucinations
Browse by: Latest US Patents, China's latest patents, Technical Efficacy Thesaurus, Application Domain, Technology Topic, Popular Technical Reports.
© 2025 PatSnap. All rights reserved.Legal|Privacy policy|Modern Slavery Act Transparency Statement|Sitemap|About US| Contact US: help@patsnap.com