Rapid drying method for cottonwood thick plate
A rapid drying, poplar technology, applied in the direction of drying solid materials, heating to dry solid materials, and promoting the preliminary treatment of solid materials drying, etc., can solve problems such as increased heat loss, reduce preheating time, increase plasticity, and improve quality effect
- Summary
- Abstract
- Description
- Claims
- Application Information
AI Technical Summary
Problems solved by technology
Method used
Examples
Embodiment 1
[0029] Poplar, initial moisture content is 120%, thickness 5.0cm, adopts the rapid drying method of poplar plank of the present invention to carry out drying treatment.
[0030] 1) Palletizing
[0031] Make poplar stacks with a length of 3.0m, a width of 1.6m, and a height of 1.4m. Close the gate.
[0032] 2) poplar wood pretreatment
[0033] The heated humid air is fed into the pretreatment kiln through the circulating fan, and the steam spraying treatment starts when the temperature of the incoming material stack reaches 60°C. The temperature of the superheated steam at normal pressure is between 150°C and 160°C. At 90°C, heat preservation starts, and the heat preservation time is 1.5 hours / cm, that is, 7.5 hours. After the treatment, the poplar is taken out of the kiln for drying. When leaving the kiln, the moisture content can be reduced to 60% to 80%.
[0034] 3) poplar wood drying
[0035] The treated poplar is correctly stacked in the drying kiln according to the ...
Embodiment 2
[0041] Poplar, initial moisture content is 140%, thickness 7.0cm, adopts the rapid drying method of poplar plank of the present invention to carry out drying treatment.
[0042] 1) Palletizing
[0043] Make poplar stacks with a length of 3.0m, a width of 1.8m, and a height of 1.6m. Close the gate.
[0044] 2) poplar wood pretreatment
[0045] The heated humid air is introduced into the pretreatment kiln through the circulating fan, and the steam spraying treatment starts when the temperature of the incoming material pile reaches 60°C, the temperature of the superheated steam at normal pressure is between 140°C and 150°C, when the temperature of the wood core reaches 60°C At 90°C, heat preservation starts, and the heat preservation time is 2 hours / cm, that is, 14 hours. After the treatment, the poplar is taken out of the kiln for drying. When leaving the kiln, the moisture content can be reduced to 70% to 80%.
[0046] 3) poplar wood drying
[0047] The treated poplar is ...
PUM
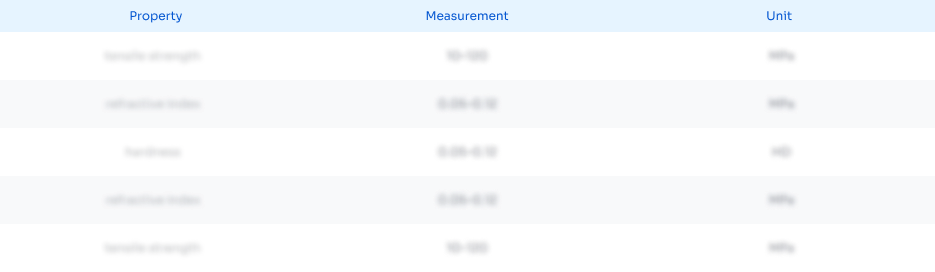
Abstract
Description
Claims
Application Information

- R&D
- Intellectual Property
- Life Sciences
- Materials
- Tech Scout
- Unparalleled Data Quality
- Higher Quality Content
- 60% Fewer Hallucinations
Browse by: Latest US Patents, China's latest patents, Technical Efficacy Thesaurus, Application Domain, Technology Topic, Popular Technical Reports.
© 2025 PatSnap. All rights reserved.Legal|Privacy policy|Modern Slavery Act Transparency Statement|Sitemap|About US| Contact US: help@patsnap.com