Waste heat recovering device of high-temperature metallurgy slag particles
A waste heat recovery device and a technology for metallurgical slag, applied in the field of waste heat recovery in the metallurgical industry, can solve the problems of secondary energy loss, high investment cost and high power consumption, improve output and quality, achieve uniform heat exchange, and strengthen horizontal mixing. heat transfer effect
- Summary
- Abstract
- Description
- Claims
- Application Information
AI Technical Summary
Problems solved by technology
Method used
Image
Examples
Embodiment Construction
[0020] The present invention will be further described below in conjunction with the accompanying drawings and embodiments.
[0021] High-temperature metallurgical slag waste heat recovery device, including intermediate hopper 2, boiler furnace body, steam drum 7, superheater 6, evaporator 8, economizer 15 and discharger 17, the intermediate hopper 2 is set at the inlet of the boiler furnace body Above, the boiler furnace body is a rectangular furnace shell 4 welded by stainless steel plates. The built-in refractory material 5 forms a rectangular cavity and is fixed on the boiler bracket 3. The boiler furnace body is divided into storage section I and working section II from top to bottom. The height of the storage section I is 1 / 4~1 / 2 of the height of the working section II, and the superheater 6, the evaporator 8, and the economizer 15 are sequentially arranged in the working section II from top to bottom, and a superheater is provided in this embodiment 6. Three evaporators...
PUM
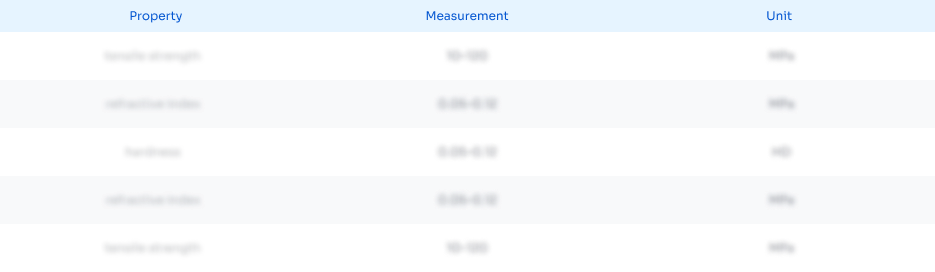
Abstract
Description
Claims
Application Information

- R&D
- Intellectual Property
- Life Sciences
- Materials
- Tech Scout
- Unparalleled Data Quality
- Higher Quality Content
- 60% Fewer Hallucinations
Browse by: Latest US Patents, China's latest patents, Technical Efficacy Thesaurus, Application Domain, Technology Topic, Popular Technical Reports.
© 2025 PatSnap. All rights reserved.Legal|Privacy policy|Modern Slavery Act Transparency Statement|Sitemap|About US| Contact US: help@patsnap.com