Method for preparing acetophenone by oxidizing ethylbenzene in continuous flow micro-channel reactor
A channel reactor, acetophenone technology, applied in the direction of oxidation to prepare carbonyl compounds, etc., can solve the problems of low conversion rate of ethylbenzene, high toxicity, low yield of acetophenone, etc., to improve reaction efficiency, precise temperature control, The effect of increasing selectivity
- Summary
- Abstract
- Description
- Claims
- Application Information
AI Technical Summary
Problems solved by technology
Method used
Image
Examples
Embodiment 1
[0027] 1. Raw material preparation: Weigh 34Kg of cobalt acetate, put it into a container with 150L of glacial acetic acid, stir to dissolve it completely, measure 150L of ethylbenzene, pour it into the container, stir, then weigh 16.24KgKBr and add a small amount Water to make it completely dissolved first, pour the completely dissolved KBr solution into the mixed solution, stir evenly, and seal it. Measure 1000L30%H 2 o 2 Put it in another container and seal it.
[0028] 2. In a T-shaped microchannel made of PFA ( image 3 Shown), the channel feature size is 3.14mm. refer to figure 1 Process flow of the present invention utilizes figure 2 The device diagram, according to the following steps: (1) the glacial acetic acid solution of ethylbenzene in the raw material tank 1 enters the microchannel reactor 8 through the pump 3, and the oxidant hydrogen peroxide in the raw material tank 2 enters the microchannel reactor 8 through the pump 4. (2) Continuous flow microchanne...
Embodiment 2
[0031] 1. Raw material preparation: Weigh 15.3Kg of cobalt nitrate, pour it into a container with 300L of acetone, stir to dissolve it completely, measure 150L of ethylbenzene, pour it into the container, stir, then weigh 8.8Kg of NaBr and add A small amount of water to make it completely dissolved first, pour the completely dissolved NaBr solution into the mixed solution, stir evenly, and seal it. Then measure 100mL70%H 2 o 2 Put it in another container and seal it.
[0032] 2. In the coil microchannel made of PFA ( image 3 Shown), the channel feature size is 2.0mm. refer to figure 2 Process flow of the present invention utilizes figure 2 The device diagram, according to the following steps: (1) the glacial acetic acid solution of ethylbenzene in the raw material tank 1 enters the microchannel reactor 8 through the pump 3, and the oxidant hydrogen peroxide in the raw material tank 2 enters the microchannel reactor 8 through the pump 4. (2) Continuous flow microchanne...
Embodiment 3
[0035] 1. Raw material preparation: Weigh 24.5Kg of cobalt acetate, pour it into a 750L container of glacial acetic acid, stir to dissolve it completely, measure 150L of ethylbenzene, pour it into the container, stir, and then weigh 16.38KgKBr Add a small amount of water to make it completely dissolved first, pour the completely dissolved KBr solution into the mixed solution, stir evenly, and seal it. Then measure 1000L80%H 2 o 2 Put it in another container and seal it.
[0036] 2. In the coiled tube microchannel made of stainless steel ( image 3 Shown), the channel feature size is 1.2mm. refer to figure 2 Process flow of the present invention utilizes figure 2 The device diagram, according to the following steps: (1) the glacial acetic acid solution of ethylbenzene in the raw material tank 1 enters the microchannel reactor 8 through the pump 3, and the oxidant hydrogen peroxide in the raw material tank 2 enters the microchannel reactor 8 through the pump 4. (2) Conti...
PUM
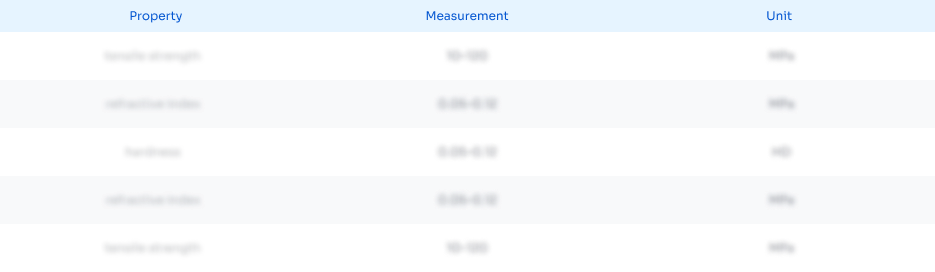
Abstract
Description
Claims
Application Information

- R&D
- Intellectual Property
- Life Sciences
- Materials
- Tech Scout
- Unparalleled Data Quality
- Higher Quality Content
- 60% Fewer Hallucinations
Browse by: Latest US Patents, China's latest patents, Technical Efficacy Thesaurus, Application Domain, Technology Topic, Popular Technical Reports.
© 2025 PatSnap. All rights reserved.Legal|Privacy policy|Modern Slavery Act Transparency Statement|Sitemap|About US| Contact US: help@patsnap.com