Electric locomotive pantograph carbon slide plate
A pantograph carbon sliding plate, electric locomotive technology, applied in the fields of subway, urban rail transit, mining locomotive, can solve the problem of high wear and tear of catenary wires, achieve long service life, prolong the repair period, and reduce the bonding resistance.
- Summary
- Abstract
- Description
- Claims
- Application Information
AI Technical Summary
Problems solved by technology
Method used
Image
Examples
Embodiment 1
[0026] Example 1: Electric locomotive pantograph carbon slide plate, made of the following raw materials in parts by weight: 5.3 parts of semi-reinforcing carbon black, 2.5 parts of -398 flake graphite, 1.8 parts of 599 flake graphite, 1 part of charcoal powder and melted coal 5.6 parts of asphalt.
[0027] The process steps of the preparation method are: (1) Thermal mixing: Add semi-reinforcing carbon black, -398 flake graphite, 599 flake graphite and charcoal powder in the above raw materials into a 500 liter kneader according to the weight ratio for thermal mixing, and heat Mix for 50-60 minutes, when the temperature is higher than 130°C, add melted coal tar pitch, then heat mix for 2-3 hours, when the temperature reaches 170-180°C, unload;
[0028] (2) Rolled sheet: control the thickness of the rolled sheet within 2mm;
[0029] (3) Grinding: use 3R pendulum mill for grinding, control particle size: -240 mesh pass rate 55-75%;
[0030] (4) Pressing: use a 500-ton hydrauli...
Embodiment 2
[0051] Embodiment 2: Electric locomotive pantograph carbon slide plate, adopt the following raw materials to make by weight: 4.3 parts of semi-reinforcing carbon black, 1.5 parts of -398 flake graphite, 0.8 part of 599 flake graphite, 0.5 part of charcoal powder and melted coal 4.6 parts of asphalt.
[0052] The preparation method is the same as in Example 1.
Embodiment 3
[0053] Embodiment 3: electric locomotive pantograph carbon slide plate, adopt the following raw materials to make by weight: 6.3 parts of semi-reinforcing carbon black, 3.5 parts of -398 flake graphite, 2.8 parts of 599 flake graphite, 1.5 parts of charcoal powder and melted coal 6.6 parts of asphalt.
[0054] The preparation method is the same as in Example 1.
[0055] Below is the inspection report of the product of the present invention by the Product Quality Supervision and Inspection Center of the Ministry of Railways:
[0056]
PUM
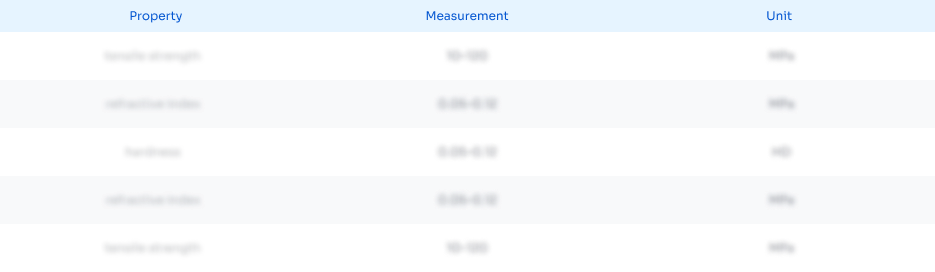
Abstract
Description
Claims
Application Information

- R&D
- Intellectual Property
- Life Sciences
- Materials
- Tech Scout
- Unparalleled Data Quality
- Higher Quality Content
- 60% Fewer Hallucinations
Browse by: Latest US Patents, China's latest patents, Technical Efficacy Thesaurus, Application Domain, Technology Topic, Popular Technical Reports.
© 2025 PatSnap. All rights reserved.Legal|Privacy policy|Modern Slavery Act Transparency Statement|Sitemap|About US| Contact US: help@patsnap.com