Production method of glass thermometer without vacuum blowing processing
A production method and technology of thermometers, applied in thermometers, thermometers based on expansion/contraction of materials, measuring devices, etc., can solve problems such as pollution, and achieve the steps of avoiding mercury evaporation pollution, reducing rising vacuum and detecting stress, and solving mercury Effects of evaporative pollution problems
- Summary
- Abstract
- Description
- Claims
- Application Information
AI Technical Summary
Problems solved by technology
Method used
Image
Examples
Embodiment 1
[0020] Step 1: Put the semi-finished thermometer tube material that has been shrinked into a tray, and perform high-temperature aging at 480°C, and keep the temperature at 480°C for 7 hours.
[0021] Step 2: Take out the tube material of the thermometer, and cool the tube material naturally to 30-40°C.
[0022] Step 3: Use a mechanical pump and a diffusion pump to evacuate the airtight chamber for 8 hours, and the vacuum degree is 2×10 -2 Pa. After reaching the required vacuum degree, liquid nitrogen was poured into the vacuum chamber for cooling treatment, and the temperature in the vacuum chamber was stabilized at 37°C. Then put the pipe material into the vacuum chamber for mercury injection, and the flow rate of mercury injection is required to be 10min / 70kg.
[0023] Step 4: The thermometer tubing after mercury injection is soaked in a constant temperature water tank with a temperature of about 42.25°C to raise the temperature. The allowable error of the water temperatur...
Embodiment 2
[0029] Step 1: Put the semi-finished thermometer tube material that has been shrunk into a tray for high-temperature aging at 440°C, and keep the temperature at 440°C for 6 hours.
[0030] Step 2: Take out the tube material of the thermometer, and cool the tube material naturally to 30-40°C.
[0031] Step 3: Use a mechanical pump and a diffusion pump to evacuate the airtight chamber for 8 hours, and the vacuum degree is 2.3×10 -2 Pa. After reaching the required vacuum degree, pour liquid nitrogen into the vacuum chamber for about 10 minutes for cooling treatment, and the temperature in the vacuum chamber is stabilized below 38°C. Then put the pipe material into the vacuum chamber for mercury injection, and the flow rate of mercury injection is required to be 30min / 70kg.
[0032] Step 4: The thermometer tubing after mercury injection is soaked in a constant temperature water tank with a temperature of about 42.25°C to raise the temperature. The allowable error of the water te...
PUM
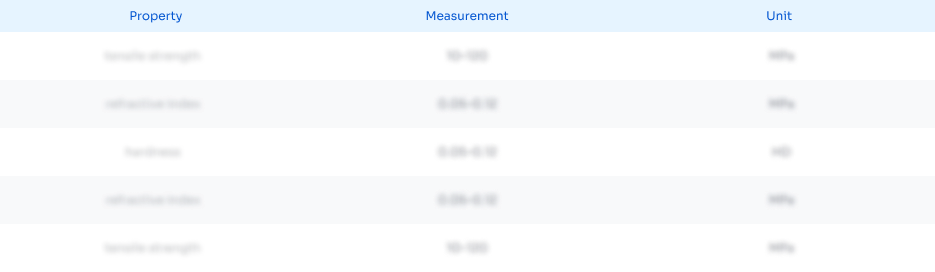
Abstract
Description
Claims
Application Information

- Generate Ideas
- Intellectual Property
- Life Sciences
- Materials
- Tech Scout
- Unparalleled Data Quality
- Higher Quality Content
- 60% Fewer Hallucinations
Browse by: Latest US Patents, China's latest patents, Technical Efficacy Thesaurus, Application Domain, Technology Topic, Popular Technical Reports.
© 2025 PatSnap. All rights reserved.Legal|Privacy policy|Modern Slavery Act Transparency Statement|Sitemap|About US| Contact US: help@patsnap.com