Thermal shock resistant thin-walled cordierite honeycomb ceramics and preparation method thereof
A technology of cordierite honeycomb and thermal shock resistance, which is applied in the field of cordierite honeycomb ceramics, can solve the problems of catalyst carrier with large specific surface area, low thermal expansion mechanical strength, and failure to meet Euro IV standards, so as to improve product survival rate, Improved blendability and improved thermal shock resistance
- Summary
- Abstract
- Description
- Claims
- Application Information
AI Technical Summary
Problems solved by technology
Method used
Image
Examples
Embodiment 1
[0032] The thermal shock-resistant thin-walled cordierite honeycomb ceramics are prepared according to the following steps.
[0033] (1) Mix bimodal α-alumina micropowder and oleic acid evenly;
[0034] (2) Mix the product obtained in step (1) with talc evenly;
[0035] (3) Mix the product obtained in step (2) with flaky kaolin, calcined kaolin, fused silica, PAO2 (a low-viscosity polyalphaolefin), methylcellulose and water;
[0036] (4) The product obtained in step (3) is molded, dried, and then sintered at a sintering temperature of 1400°C, kept at this sintering temperature for 10 hours, and then cooled to room temperature;
[0037] (5) The weight of each component in the above steps is shown in Table 1, and the unit of the data in Table 1 is kg.
[0038] Table 1
[0039]
Embodiment 2
[0041] Thermal shock-resistant thin-walled cordierite honeycomb ceramics are prepared according to the following steps:
[0042] (1) Mix bimodal α-alumina micropowder and activated alumina micropowder evenly;
[0043] (2) Mix the product obtained in step (1) with stearic acid evenly;
[0044] (3) Mix the product obtained in step (2) with talc evenly;
[0045] (4) uniformly mixing the product obtained in step (3) with flaky kaolin, calcined kaolin, fused quartz, aviation diesel, methylcellulose and water;
[0046] (5) The product obtained in step (4) is molded, dried, and then sintered at a sintering temperature of 1420°C, kept at this sintering temperature for 6 hours, and then cooled to room temperature;
[0047] (6) The weight of each component in the above steps is shown in Table 1, and the unit of the data in Table 1 is kg
Embodiment 3
[0049] Thermal shock-resistant thin-walled cordierite honeycomb ceramics are prepared according to the following steps:
[0050] (1) Mix bimodal α-alumina micropowder and activated alumina micropowder evenly;
[0051](2) Mix the product obtained in step (1) with sodium stearate evenly;
[0052] (3) Mix the product obtained in step (2) with talc evenly;
[0053] (4) uniformly mixing the product obtained in step (3) with flaky kaolin, calcined kaolin, fused quartz, corn oil, hydroxypropyl methylcellulose and water;
[0054] (5) The product obtained in step (4) is molded, dried, and then sintered at a sintering temperature of 1390°C, kept at this sintering temperature for 12 hours, and then cooled to room temperature;
[0055] (6) The weight of each component in the above steps is shown in Table 1, and the unit of the data in Table 1 is kg.
[0056] The detection performance of the thermal shock-resistant thin-walled cordierite honeycomb ceramics prepared in Examples 1-3 is sh...
PUM
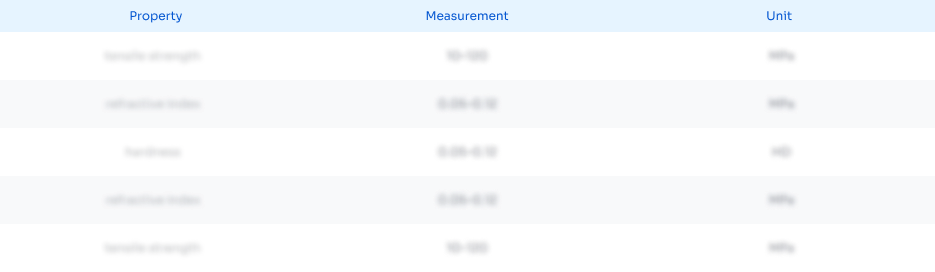
Abstract
Description
Claims
Application Information

- Generate Ideas
- Intellectual Property
- Life Sciences
- Materials
- Tech Scout
- Unparalleled Data Quality
- Higher Quality Content
- 60% Fewer Hallucinations
Browse by: Latest US Patents, China's latest patents, Technical Efficacy Thesaurus, Application Domain, Technology Topic, Popular Technical Reports.
© 2025 PatSnap. All rights reserved.Legal|Privacy policy|Modern Slavery Act Transparency Statement|Sitemap|About US| Contact US: help@patsnap.com