Method for recovering valuable metal from electroplating sludge
A technology of electroplating sludge and valuable metals, applied in the direction of improving process efficiency, etc., can solve problems such as poor economic benefits, environmental pollution, loss of metal resources, etc., achieve significant economic and social benefits, easy control of process conditions, The effect of high purity of recycled products
- Summary
- Abstract
- Description
- Claims
- Application Information
AI Technical Summary
Problems solved by technology
Method used
Image
Examples
Embodiment 1
[0035] see figure 1 , the present embodiment production method is as follows:
[0036] Step 1: Put 500 grams of electroplating sludge raw materials (Ni5.6%, Cu7.8%, Cr3.88%, Zn3.12%, Fe1.29%) in a 3000ml beaker, with a 2:1 liquid-solid Then, slowly add concentrated sulfuric acid while stirring, and stop adding acid when the pH is stable at 1.5; then turn on the electric furnace to raise the temperature to 75°C, and under the condition of about 75°C, properly replenish acid to maintain pH = 1.5 remains the same, continue to decompose for 60 minutes; then carry out pressure filtration, the pressure filtration filtrate enters the next process to continue processing, the pressure filtration filter residue is washed, the washing water is returned to the previous process for pulping water, and the residue after washing is solidified.
[0037] Step 2: Put 1600ml of the solution prepared in step 1 into a 3000ml beaker, start stirring, and heat to 85°C. 2+ : NaClO 3 = Add sodium chl...
Embodiment 2
[0044] see figure 1 , the present embodiment production method is as follows:
[0045] Step 1: Put 500 grams of electroplating sludge raw materials (Ni3.5%, Cu1.2%, Cr6.43%, Zn1.12%, Fe2.01%) in a 3000ml beaker, with 3:1 liquid-solid Then, slowly add concentrated sulfuric acid while stirring. When the pH is stable at 1.5, stop adding acid; turn on the electric furnace and raise the temperature to 80°C. Change, continue to decompose for 1 hour; press filtration, the filtrate enters the next process to continue processing, the filter residue is washed, the washing water is returned to the previous process for pulping water, and the washed residue is solidified;
[0046] Step 2: Put 1600ml of the solution prepared in step 1 into a 3000ml beaker, start stirring, and heat to 90°C. 2+ : NaClO 3 = Add 10ml of sodium chlorate at a ratio of 6:0.5. After reacting for 20 minutes, slowly add 30% sodium carbonate solution while stirring. When the pH=4 or so, stop adding sodium carbonate...
Embodiment 3
[0053] see figure 1 , the present embodiment production method is as follows:
[0054] Step 1: Put 500 grams of electroplating sludge raw materials (Ni 3.45%, Cu 8.7%, Cr 5.69%, Zn 1.5%, Fe 2.31%) into a 3000ml beaker, and make a slurry with a liquid-solid ratio of 4:1 Then, slowly add concentrated sulfuric acid while stirring, when the pH is stable at 1.5, stop adding acid; turn on the electric furnace and heat up to 80°C, and under the condition of 80°C, add acid appropriately to keep pH = 1.5, and continue to decompose 80 minutes; then carry out pressure filtration, the pressure filtration filtrate enters the next process to continue processing, the pressure filtration filter residue is washed, and the washing water is returned as slurry mixing water, and the residue after washing is solidified;
[0055] Step 2: Put 1600ml of the solution prepared in step 1 into a 3000ml beaker, start stirring, and heat to 95°C. 2+ : NaClO 3 Add sodium chlorate in the ratio of =6:0.6 to ...
PUM
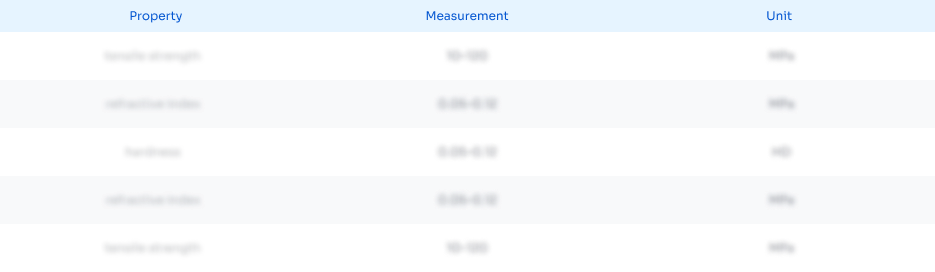
Abstract
Description
Claims
Application Information

- Generate Ideas
- Intellectual Property
- Life Sciences
- Materials
- Tech Scout
- Unparalleled Data Quality
- Higher Quality Content
- 60% Fewer Hallucinations
Browse by: Latest US Patents, China's latest patents, Technical Efficacy Thesaurus, Application Domain, Technology Topic, Popular Technical Reports.
© 2025 PatSnap. All rights reserved.Legal|Privacy policy|Modern Slavery Act Transparency Statement|Sitemap|About US| Contact US: help@patsnap.com