Plasma etching method for fabricating uniform fine patterns
A plasma and plasma source technology, applied in the field of plasma etching, can solve the problems of pattern collapse, long cutting time, small cutting size range, etc., to minimize the difference of feature size, ensure stability and uniformity The effect of hyperfine structure
- Summary
- Abstract
- Description
- Claims
- Application Information
AI Technical Summary
Problems solved by technology
Method used
Image
Examples
Embodiment Construction
[0024] The specific embodiment of the present invention will be further described below in conjunction with accompanying drawing:
[0025] The invention discloses a plasma etching method for making a uniform fine pattern, wherein, the one-step cutting process adopted in the prior art, since any kind of mixed gas is used as the plasma source will result in dense areas and open areas The feature difference is large, so the present invention uses different gas mixtures for multi-step cutting, so that the feature size difference between the dense area and the empty area is reduced.
[0026] figure 1 It is a flow chart of the plasma etching method for making a uniform fine pattern in the present invention, please refer to figure 1 , the specific process flow adopted by the present invention is, in the process of semiconductor cutting process, adopt step A201: use the first gas as the plasma source to carry out the cutting of the hard mask layer; step B202: carry out the curing of ...
PUM
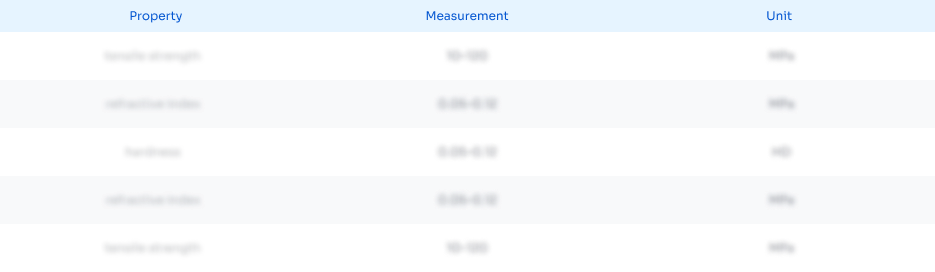
Abstract
Description
Claims
Application Information

- R&D
- Intellectual Property
- Life Sciences
- Materials
- Tech Scout
- Unparalleled Data Quality
- Higher Quality Content
- 60% Fewer Hallucinations
Browse by: Latest US Patents, China's latest patents, Technical Efficacy Thesaurus, Application Domain, Technology Topic, Popular Technical Reports.
© 2025 PatSnap. All rights reserved.Legal|Privacy policy|Modern Slavery Act Transparency Statement|Sitemap|About US| Contact US: help@patsnap.com