Etching Agent Composite Used For Etching Conductive Multi-layer Film And Etching Method Using The Same
A technology of composition and etchant, which is applied in the direction of surface etching composition, chemical instruments and methods, circuits, etc., can solve problems such as rising demand for metallization layers, and achieve the effect of simplifying production cost and time, and reducing process
- Summary
- Abstract
- Description
- Claims
- Application Information
AI Technical Summary
Problems solved by technology
Method used
Image
Examples
experiment Embodiment 1
[0058] A Cu / Mo bilayer film was deposited on a substrate and a photoresist (PR) was formed thereon to fabricate a sample. The etchant of Example 1 and Comparative Example 1 were each placed in a spray type etching system (FNS Tech.) and heated to 40°C. When the temperature reaches 40±0.1°C, etchant is used to etch the Cu / Mo bilayer film. Etch times were over 50% etch with endpoint detection (EPD). After the etching was completed, the substrate was taken out of the etching system, washed with deionized water, and dried using a hot air dryer. Use a photoresist stripper to remove the photoresist. Critical dimension (CD) skew (etch loss), step length as a width difference between copper and molybdenum layers, and etch residue of etched structures were evaluated using scanning electron microscopy (SEM, TESCAN).
Embodiment 1
[0061]Specifically, KR 2006-0082270 A discloses an etchant composition for etching metal electrodes to form thin film transistors for flat panel displays. In addition to phosphoric acid, nitric acid, acetic acid, and water, which are components of a typical etchant for etching aluminum, the etchant composition contains an etch rate control agent to form a desired pattern. According to Example 1 of this prior art, the etchant has the following composition:
[0062] h 3 PO 4 (55% by weight)+HNO 3 (8% by weight)+CH3COOH (10% by weight)+(NH 4 ) 2 HPO 4 (2wt%)+CH 3 COONH 4 (2% by weight)+H 2 O (surplus).
[0063] The etching properties of the etchant were tested. The results are shown in Figure 1a and 1b middle.
[0064] specifically, Figure 1a Shows the detailed results obtained when applying the etchant of Comparative Example 1 to a Cu / Mo bilayer film as proposed in the prior art (KR 2006-0082270 A) embodiment comprising phosphoric acid, nitric acid , acetic acid a...
Embodiment 2
[0073] h 3 PO 4 (70% by weight)+HNO 3 (2wt%)+CH 3 COOH (15% by weight) + imidazole (C 3 h 4 N 2 , 0.1 to 0.3% by weight) + distilled water (balance).
PUM
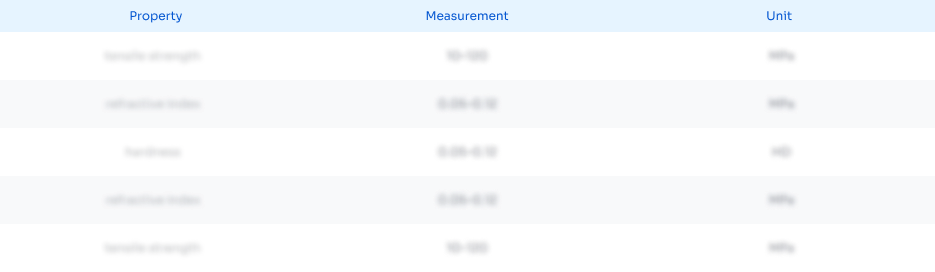
Abstract
Description
Claims
Application Information

- Generate Ideas
- Intellectual Property
- Life Sciences
- Materials
- Tech Scout
- Unparalleled Data Quality
- Higher Quality Content
- 60% Fewer Hallucinations
Browse by: Latest US Patents, China's latest patents, Technical Efficacy Thesaurus, Application Domain, Technology Topic, Popular Technical Reports.
© 2025 PatSnap. All rights reserved.Legal|Privacy policy|Modern Slavery Act Transparency Statement|Sitemap|About US| Contact US: help@patsnap.com