Method for the preparation of alkyl levulinates
A technology of alkyl levulinate and alkyl, which is applied in the field of preparing alkyl levulinate, can solve problems such as loss of catalytic activity, achieve good safety, avoid equipment corrosion, and avoid the effects of by-product formation
- Summary
- Abstract
- Description
- Claims
- Application Information
AI Technical Summary
Problems solved by technology
Method used
Image
Examples
Embodiment 1
[0107] A 250 mL 3-necked flask equipped with a magnetic stirring bar, a thermocouple, a condenser and a rubber septum was charged with 100 mL of ethyl levulinate (obtained from Langfang Triple Well Chemicals Company, Ltd., Langfang, Hebei Province, China) and 5 mL of ethanol (100% , obtained from Sigma-Aldrich, St. Louis, MO). The flask was heated to reflux using a heating mantle. The boiling point stabilized at 154.2°C within 25 minutes. At 10 minute intervals, three consecutive 5 mL aliquots of ethanol were added to the flask through a rubber septum using a syringe and the boiling point was recorded. Finally, 1 mL of deionized water was added to the flask through the rubber. The boiling point was recorded after 10 minutes. Table 1 shows the recorded boiling points of the mixtures.
[0108]
[0109] Table 1. Boiling points of ethanol / ethyl levulinate mixture diaphragms.
Embodiment 2
[0111] A 500mL 3-necked flask was equipped with a magnetic stirring bar, dropping funnel, condenser and thermocouple. The flask was charged with 100.06g (0.694mol) ethyl levulinate (from Langfang Triple Well Chemicals Company, Ltd., Langfang City, Hebei Province, China) 11.48g (0.249mol) ethanol (99.5+%, from Acros Organics of Geel, Belgium) and sulfuric acid solution (prepared by mixing 0.575 mL concentrated sulfuric acid in 1.463 mL deionized water). The mixture was stirred and heated to reflux at 107.0°C in a 120°C oil bath. A mixture of 49.23 g (0.497 mol) furfuryl alcohol (99%, from Acros Organics) and 31.50 g (0.684 mol) ethanol was added dropwise to the reaction mixture over 108 minutes. After the addition was complete, the reaction was refluxed for another 1 h. The reaction flask was removed from the oil bath and allowed to cool to ambient temperature.
[0112] A sample of the crude reaction mixture was removed for analysis. The crude reaction product was dissolved...
Embodiment 3
[0115] A 500 mL 3-neck flask equipped with a magnetic stirring bar, dropping funnel, condenser and thermocouple was charged with 100.21 g (0.695 mol) ethyl levulinate (obtained from Langfang Triple Well Chemicals Company, Ltd., Langfang, Hebei Province, China) , 7.60 g (0.165 mol) of ethanol (99.5+%, from Acros Organics of Geel, Belgium) and sulfuric acid solution (prepared by mixing 0.575 mL of concentrated sulfuric acid in 1.463 mL of deionized water). The mixture was stirred and heated to reflux at 116.3°C in a 135°C oil bath. A mixture of 49.12 g (0.496 mol) furfuryl alcohol (99%, from Acros Organics) and 28.72 g (0.624 mol) ethanol was added dropwise to the reaction mixture over 115 minutes. After the addition was complete, the reaction was refluxed for another 1 h. The reaction flask was then removed from the oil bath and allowed to cool to room temperature.
[0116] About 50.445 g of the reaction mixture was transferred to a 250 mL flask and distillation was performed...
PUM
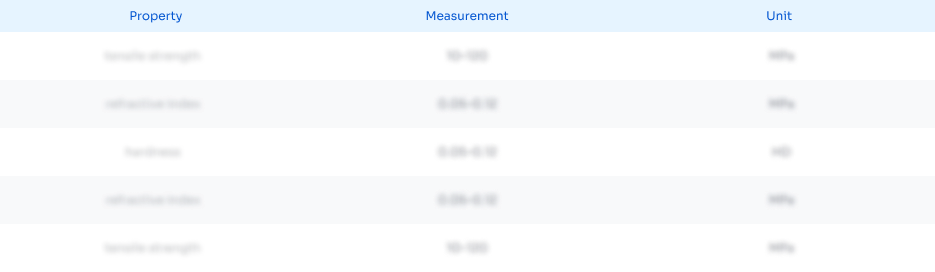
Abstract
Description
Claims
Application Information

- R&D
- Intellectual Property
- Life Sciences
- Materials
- Tech Scout
- Unparalleled Data Quality
- Higher Quality Content
- 60% Fewer Hallucinations
Browse by: Latest US Patents, China's latest patents, Technical Efficacy Thesaurus, Application Domain, Technology Topic, Popular Technical Reports.
© 2025 PatSnap. All rights reserved.Legal|Privacy policy|Modern Slavery Act Transparency Statement|Sitemap|About US| Contact US: help@patsnap.com