Manufacturing method and product of power connector with wires
A power connector and manufacturing method technology, which is applied in the manufacturing of contacts, circuit/collector parts, contact boxes/bases, etc., can solve the problems of high manufacturing cost, multiple quality of stations, and difficult control.
- Summary
- Abstract
- Description
- Claims
- Application Information
AI Technical Summary
Problems solved by technology
Method used
Image
Examples
specific Embodiment example 1
[0048] first as Figure 5 , on the thin metal strip (201), stamping and forming a plurality of hardware terminals (20) to form a product strip, so that each of the hardware terminals (20) has a hollow conductive pin part (202), a Conductive ring (203), a bundle of wire rings (204), and a joint (205), and the joints (205) of each hardware terminal (20) are still connected to the metal strip (201); prepare two Connecting wires, the conductive core material (301) of each connecting wire (30) is coated with an insulating coating material (302), and at least one end of the connecting wire (30) has no insulating coating and exposes the conductive core material (301);
[0049] Use riveting equipment such as a terminal crimping machine to crimp the bare conductive core material (301) at one end of the connecting wire (30) to the conductive ring (202) of the hardware terminal (20), and crimp the wire harness of the hardware terminal (20) ring (203) to bind the insulating coating materia...
specific Embodiment example 2
[0052] first as Figure 14 , on the thin metal strip (201), stamping and forming a plurality of hardware terminals (20) to form a product strip, so that each of the hardware terminals (20) has a hollow conductive pin part (202), a Conductive ring (203), a bundle of wire rings (204), two positioning elastic pieces (206) and a junction (205), and the junction (205) of each hardware terminal (20) is still connected with the metal strip (201 ) connected; prepare two connecting wires, make the conductive core material (301) of each connecting wire (30) coated with insulating coating material (302), and wherein at least one end has no insulating coating and exposes the conductive core material (301);
[0053] Use riveting equipment such as a terminal crimping machine to crimp the bare conductive core material (301) at one end of the connecting wire (30) to the conductive ring (202) of the hardware terminal (20), and crimp the wire harness of the hardware terminal (20) ring (203) to...
PUM
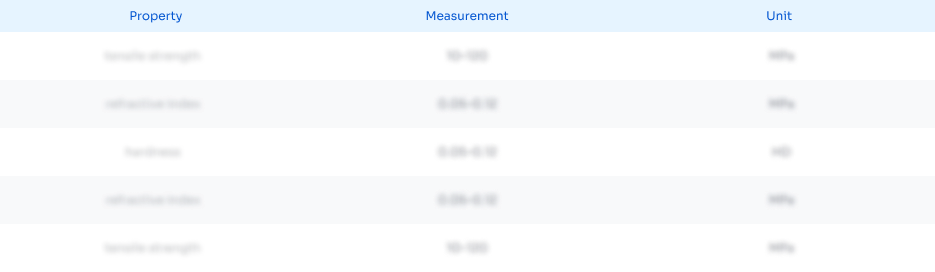
Abstract
Description
Claims
Application Information

- Generate Ideas
- Intellectual Property
- Life Sciences
- Materials
- Tech Scout
- Unparalleled Data Quality
- Higher Quality Content
- 60% Fewer Hallucinations
Browse by: Latest US Patents, China's latest patents, Technical Efficacy Thesaurus, Application Domain, Technology Topic, Popular Technical Reports.
© 2025 PatSnap. All rights reserved.Legal|Privacy policy|Modern Slavery Act Transparency Statement|Sitemap|About US| Contact US: help@patsnap.com