Preparation method of calcium ion exchange type aluminosilicate anticorrosive and anticorrosive paint
An aluminosilicate, anti-corrosion and anti-rust technology, used in alkali metal silicate coatings, anti-corrosion coatings, silicates, etc. The effect of stable basic structure, low price, high efficiency and corrosion resistance
- Summary
- Abstract
- Description
- Claims
- Application Information
AI Technical Summary
Problems solved by technology
Method used
Examples
Embodiment 1
[0017] Weigh about 10g of attapulgite, add 200ml of saturated sodium chloride solution, react in a boiling water bath, stop stirring after 1h, let it settle and filter, wash with deionized water, centrifuge for 20min, add saturated chlorine to the precipitate again Sodium chloride solution for reaction, so repeated 3 times to get sodium attapulgite.
[0018] Add 100 ml of 0.5 mol / L ammonium chloride solution to the obtained sodium attapulgite, boil in a boiling water bath for 20 minutes, settle and filter, wash with deionized water, and centrifuge for 20 minutes to obtain ammonium attapulgite.
[0019] Add the ammonium-type attapulgite to saturated lime water, boil in a boiling water bath for 24 hours, let it settle and filter, centrifuge in a centrifuge for 10 minutes, wash and dry at 100°C for 3 hours to obtain calcium-exchanged zeolite. The exchange volume is 14.69%.
Embodiment 2
[0021] Weigh about 10g of feldspar, add 200ml of 0.5mol / L sodium nitrate solution, react in a boiling water bath, stop stirring after 3 hours, let it settle and filter, wash with deionized water, centrifuge for 30min, and add the precipitate again Sodium nitrate solution for reaction, so repeated 3 times to get sodium feldspar.
[0022] Add 100 ml of 1 mol / L ammonium nitrate solution to the obtained sodium-type feldspar, boil in a boiling water bath for 30 minutes, settle and filter, wash with deionized water, and centrifuge for 30 minutes to obtain ammonium-type feldspar.
[0023] Add saturated lime water to the obtained ammonium feldspar, boil in a boiling water bath for 36 hours, settle and filter, centrifuge in a centrifuge for 20 minutes, wash and dry for 3 hours to obtain calcium-exchanged feldspar with a calcium ion exchange capacity of 15.53 %.
Embodiment 3
[0025] Weigh about 10g of zeolite, add 300ml of saturated sodium chloride solution, react in a boiling water bath, stop stirring after 4 hours, let it settle and filter, wash with deionized water, centrifuge for 20min, and add the precipitate to the sodium chloride solution again The reaction was repeated four times to obtain sodium zeolite.
[0026] Add 100 ml of 1 mol / L ammonium nitrate solution to the obtained sodium zeolite, boil in a boiling water bath for 30 minutes, settle and filter, wash with deionized water, and centrifuge for 20 minutes to obtain ammonium zeolite.
[0027] Add saturated lime water to the obtained ammonium-type zeolite, boil in a boiling water bath for 48 hours, settle and filter, centrifuge in a centrifuge for 20 minutes, wash and dry for 3 hours to obtain calcium-exchanged zeolite with a calcium ion exchange capacity of 20.79%.
PUM
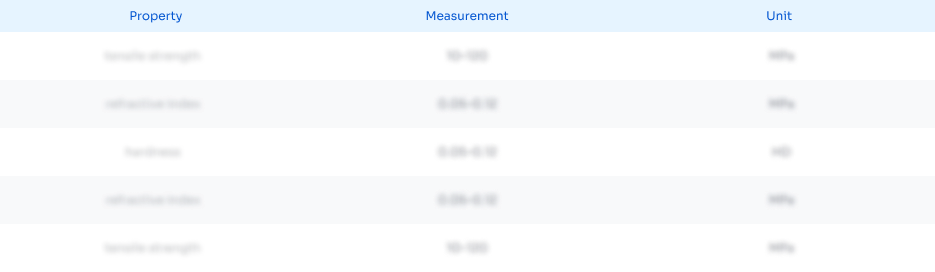
Abstract
Description
Claims
Application Information

- R&D
- Intellectual Property
- Life Sciences
- Materials
- Tech Scout
- Unparalleled Data Quality
- Higher Quality Content
- 60% Fewer Hallucinations
Browse by: Latest US Patents, China's latest patents, Technical Efficacy Thesaurus, Application Domain, Technology Topic, Popular Technical Reports.
© 2025 PatSnap. All rights reserved.Legal|Privacy policy|Modern Slavery Act Transparency Statement|Sitemap|About US| Contact US: help@patsnap.com