Method for preparing o-anisidine by catalytic hydrogenation
A technology for o-anisole and o-nitroanisole, which is applied in the field of catalytic hydrogenation to prepare o-anisole, can solve the problems of high energy consumption, large amount of waste liquid, low product yield and the like, and achieves low energy consumption. consumption, high product quality and high yield
- Summary
- Abstract
- Description
- Claims
- Application Information
AI Technical Summary
Problems solved by technology
Method used
Image
Examples
example 1
[0022] 76.5g (0.5mol) of o-nitroanisole, 76.5g of methanol, 2.3g of catalyst Raney-Ni (3% in W%) were added to a 1L autoclave. Control the reaction pressure at 1-1.2MPa, and the reaction temperature at 50-60°C. After 4 hours of reaction, take a sample to detect 99.5% of GC anthranil.
[0023]
example 2
[0025] Add 153g of o-nitroanisole (1.0mol), 153g of methanol, 4.6g of catalyst Raney-Ni (3% in W%) into a 1L high-pressure reactor, and after nitrogen replacement for 3 times, start to raise the temperature and introduce hydrogen to control the reaction The pressure is 1-1.2MPa, the reaction temperature is between 50-60°C, after 4 hours of reaction, a sample is taken to detect 99.4% of GC anthranil, and after recovery of methanol, 115g of light yellow liquid is obtained by rectification under reduced pressure, with a yield of 93.4% , GC99.5% was detected.
[0026]
example 3
[0028] Add 306g of o-nitroanisole (2.0mol), 306g of methanol, 10.2g of catalyst Raney-Ni (3% in W%) into a 1L high-pressure reactor, and after nitrogen replacement for 3 times, start to raise the temperature and introduce hydrogen to control the reaction The pressure is 1-1.2MPa, the reaction temperature is between 50-60°C, and after 4 hours of reaction, a sample is taken to detect 99.5% of GC anthranil, and after recovery of methanol, 236g of light yellow liquid is obtained by rectification under reduced pressure, with a yield of 99.59% , GC99.6% was detected.
[0029]
PUM
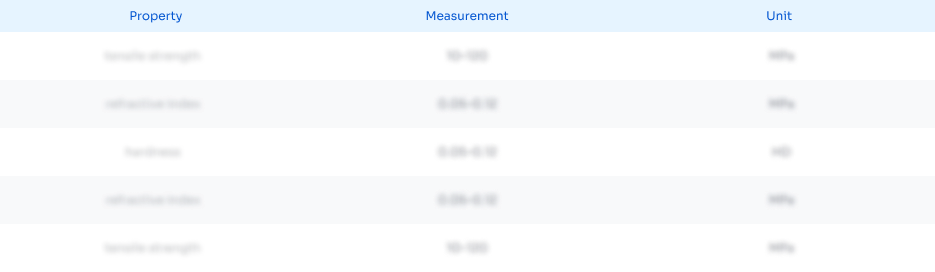
Abstract
Description
Claims
Application Information

- Generate Ideas
- Intellectual Property
- Life Sciences
- Materials
- Tech Scout
- Unparalleled Data Quality
- Higher Quality Content
- 60% Fewer Hallucinations
Browse by: Latest US Patents, China's latest patents, Technical Efficacy Thesaurus, Application Domain, Technology Topic, Popular Technical Reports.
© 2025 PatSnap. All rights reserved.Legal|Privacy policy|Modern Slavery Act Transparency Statement|Sitemap|About US| Contact US: help@patsnap.com